Polyketon solves problems where others fail
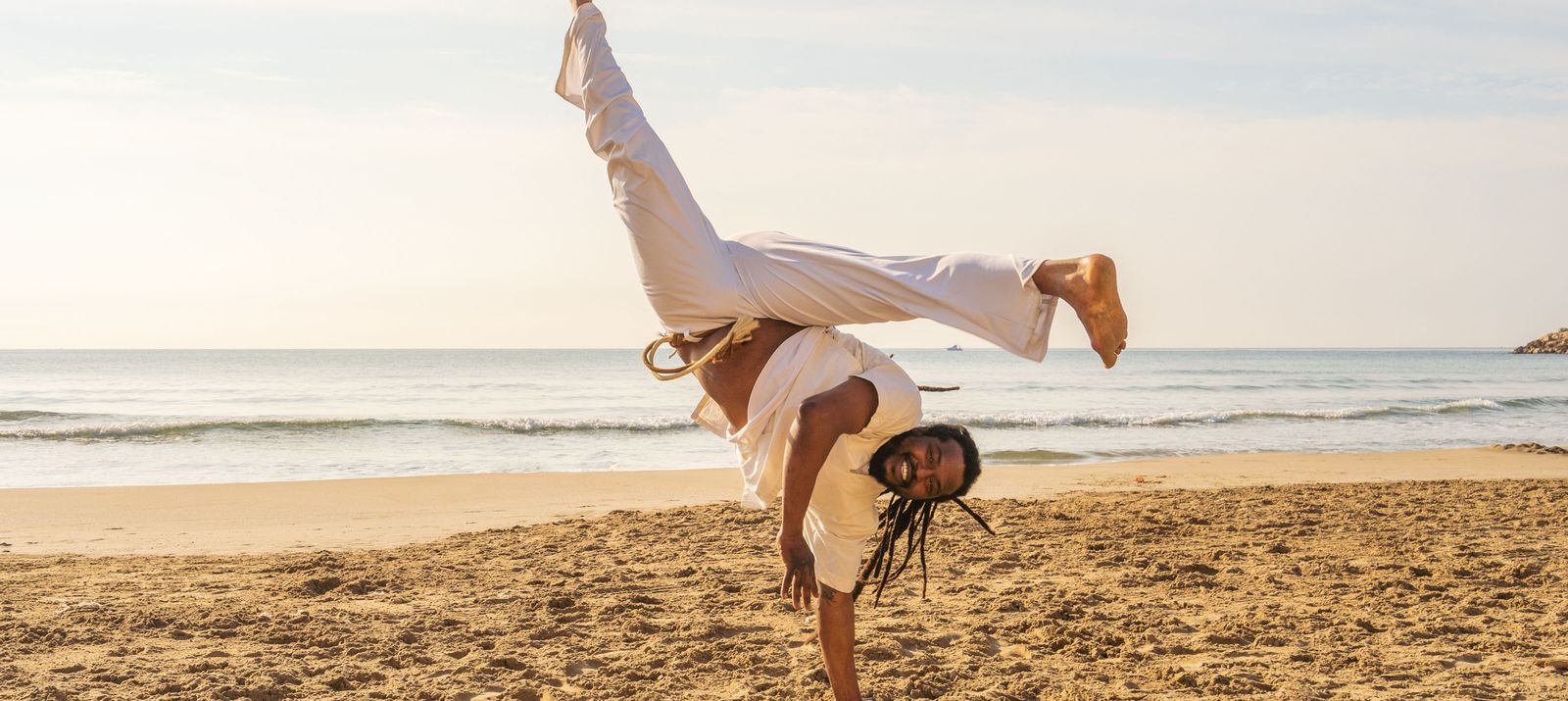
AKROTEK® PK: The revolution for your application
An aliphatic polyketone (PK) is a thermoplastic polymer with a melting point of 220°C.
PK is characterized by a number of distinctive properties and is becoming increasingly popular due to its environmental friendliness compared to other plastics. This is because it contains carbon monoxide (CO) as a comonomer. Carbon monoxide is an industrial waste gas that contributes to global warming. However, by using CO in the structure of polyketone, this gas is bound and converted into a useful monomer.
Selection of characteristic properties:
good resistance to chemicals and hydrolysis
reduced moisture absorption
short cycle times due to rapid crystallization
good tribological properties
low CO2 footprint
AKROTEK® PK
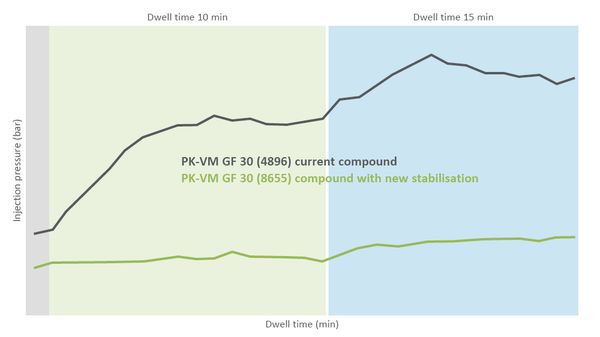
Process optimized compounds
Polyketone tends to thermo-oxidative degradation and / or crosslinking reactions under excessive thermal stress. This can be recognized by an increase in viscosity and / or the appearance of dark spots in natural colored compounds. During the injection molding process, a residence time of 10 minutes should not be exceeded.
AKRO-PLASTIC succeeded in developing a product series, which is characterized by a larger process window during processing. As you can see from the graph, the injection pressure of the currently available AKROTEK® PK-VM GF 30 black (4896) increases continuously with the increase of the dwell time in the injection molding unit and has reached a pressure maximum at a dwell time of 10 min. The optimized variant with improved stabilization, AKROTEK® PK-VM GF 30 black (8655), exhibits an almost constant injection pressure over a wide dwell time range.
High technical and flame-retardant products with improved CO2 footprint
Flame-retardant polyketone
Special requirements in e-mobility regarding flame retardancy, mechanics, chemical resistance, electrical properties, colour stability, processability and sustainability pose major challenges for a compound. AKROTEK® PK-VM GF 30 FR orange (8537) is the product of choice for e-mobility applications, e.g. battery management, MEB connectors, cable ducts and more.
The AKROTEK® PK-VM GF 30 FR meets the highest flammability requirements and is UL listed in all colours V0 from @ 0.8mm including RTI listing. AKRO uses only the most advanced flame-retardant systems that are free of red phosphorus and halogens. The requirements of high voltage components, such as bus bars, require a CTI of 600 V, which AKROTEK®PK-VM GF 30 FR orange (8537) meets.
The required colour stability and laser marking of the e-mobility industry can be realised by this material.
The process optimised AKROTEK® PK product portfolio offers injection moulders a wider processing window and more flexibility in processing.
AKROTEK® PK-VM GF 30 FR was developed for injection moulding and can also be processed on a large scale in 3D printing using pellet extrusion in additive manufacturing. See the video below.

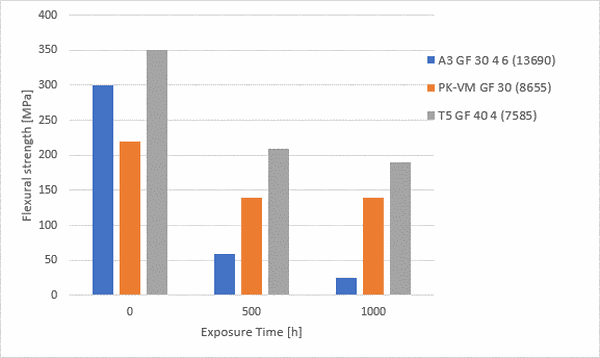
Flexural strength after storage in G12evo/water (50:50) at 135 degrees in accordance with VW TL 52682
Hydrolysis resistance
Compared to A3 GF 30 4 6 (13690), PK-VM GF 30 (8655) shows only a minimal reduction in material strength after 1000 hours. This reduction hardly affects the performance.
The natural resistance of polyketone to water glycol opens up a clear advantage in terms of component geometry design. As a result, thin-walled components can be easily realized at constant pressure ratios in the component without having to compromise on structure or performance. This opens up new possibilities for efficient and lighter designs, which is an important factor in various industries. Another advantage is the high weld line strength under pressure in water/glycol, even at elevated temperatures. These properties make PK a versatile and high-performance material, especially in applications that require robust components in various environmental conditions.
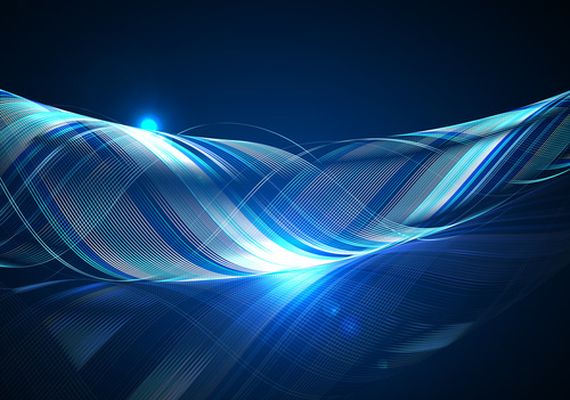
Chemical Resistance
The outstanding chemical resistance of polyketones (PK) is based on their semi-crystalline structure. Approximately half of their chemical components are derived from carbon monoxide, and a comparable structure is difficult to find in conventional chemicals and solvents. Therefore, polyketones exhibit excellent resistance to chemical influences.
The table illustrates that PKs demonstrate remarkable resistance to dissolution, degradation, and swelling when in contact with various chemicals. Neither fuels nor halogenated or aromatic hydrocarbons significantly affect their mechanical properties. Materials with hydrogen bonding, such as water, methanol, and ethanol, only cause slight swelling.
Of particular note is that solvents with similar chemical compositions, especially ketones and esters, only induce minimal swelling. In contrast to polyamides like PA6 and PA 6.6, polyketone shows pronounced resistance to aqueous media, including weak acids and bases. However, PK is less resistant to strong acids and bases, especially under elevated temperature and prolonged exposure.
Show more
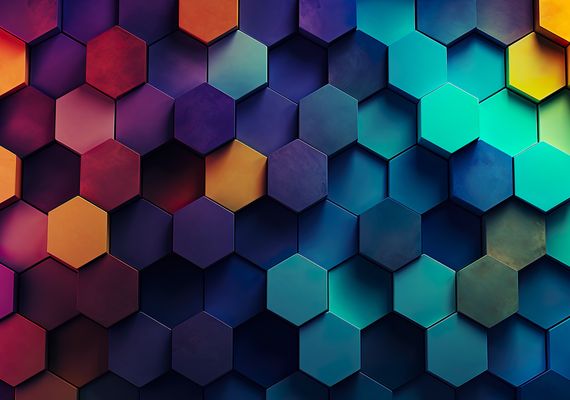
Polyketone based on masterbatches
Due to the outstanding characteristic properties of polyketone (PK), such as high load-bearing capacity, reduced moisture absorption, good tribological properties, shorter cycle times and, finally, higher environmental compatibility compared to polymer types such as polyamide (PA), polybutylene terephthalate (PBT) or polyoxymethylene (POM), polyketone has been experiencing a renaissance for some time now.
AF-COLOR has developed a masterbatch series for polyketone based on polyketone so that these properties are not influenced by the addition of another type of polymer.
A selection of the "ready to use" colors already developed can be found in the table below.
Video
Marc Ollig talks about AKROTEK® PK: Watch the Video!
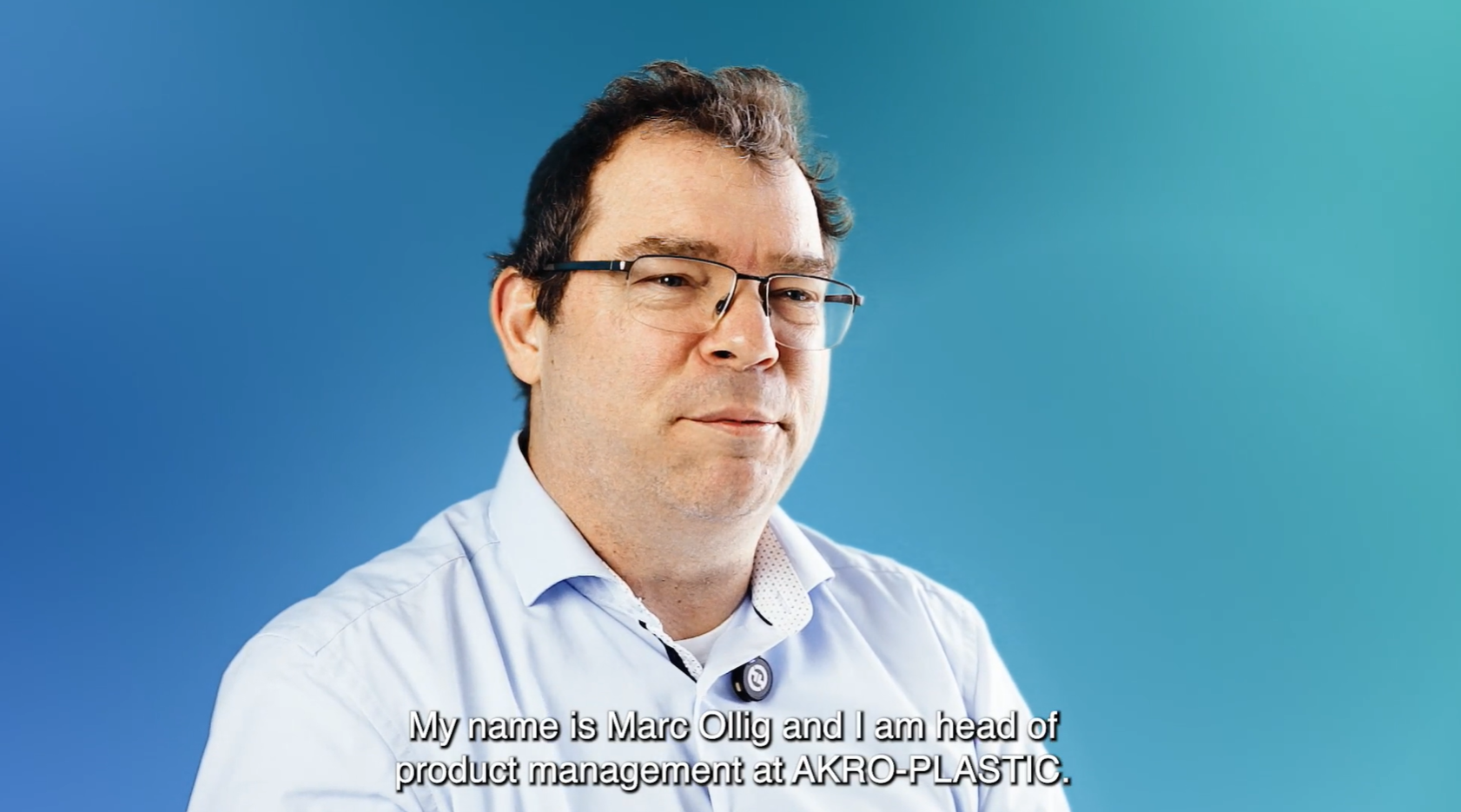
Applications
AKROTEK® PK demonstrates its diversity in various industries. The main markets served by AKROTEK® PK include the automotive, furniture and food industries as well as mechanical engineering. Explore the universal properties of polyketone and its multiple applications.
Disclaimer: All specifications and information given on this website are based on our current knowledge and experience. A legally binding promise of certain characteristics or suitability for a concrete individual case cannot be derived from this information. The information supplied here is not intended to release processors and users from the responsibility of carrying out their own tests and inspections in each concrete individual case. AKROMID®, AKROLEN®, AKROLOY®, AKROTEK®, ICX®, PRECITE® and DIA(hr)LOG® are registered trademarks of AKRO-PLASTIC GmbH.
Talk to Our Experts
With a worldwide network of plastics distribution experts, we can provide you with support anywhere in the world. Talk to one of our specialists to find out more.
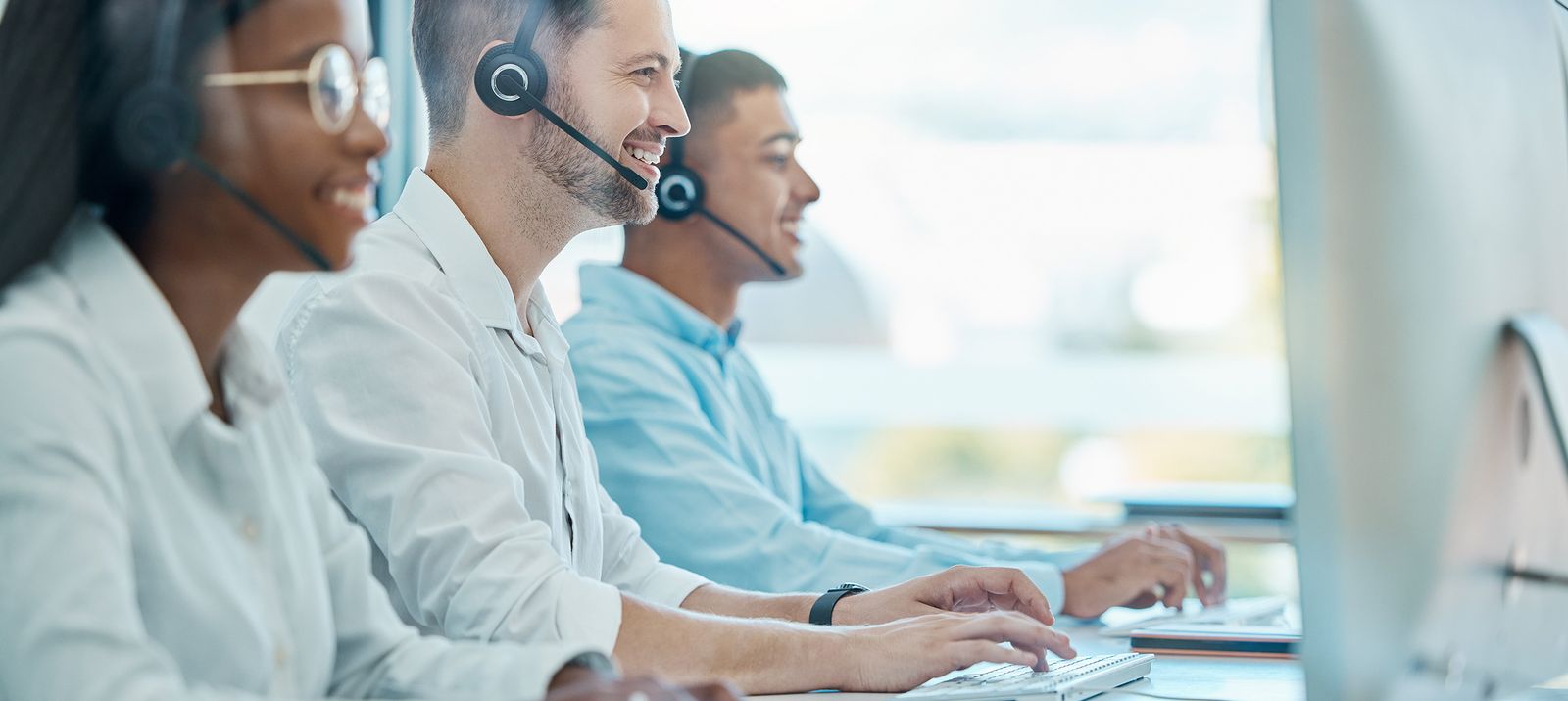