Radiator module
)
SPE Award 2024 - 2nd place in the “New Mobility” category
Revolutionary cooling module for modern vehicle systems
Vehicle manufacturer: Porsche AG
Raw material manufacturer: AKRO-PLASTIC GmbH
Parts manufacturer: SOGEFI GROUP
Other participants: Porsche AG
Sogefi, in cooperation with Porsche, has developed an innovative cooling module that meets the increasing demands of modern vehicle systems. With increased system pressure and a remarkable service life of over 30,000 hours - compared to the usual 3,000 - 5,000 hours for combustion engines - a robust and durable cooling system was essential.
Unlike conventional combustion engines, electric vehicles require the selective heating or cooling of specific components, depending on weather conditions and operating requirements. To optimize energy efficiency, each cooling unit is managed autonomously, with individual components activated when required. This is achieved by integrating a sophisticated cooling valve with over 26 connections.
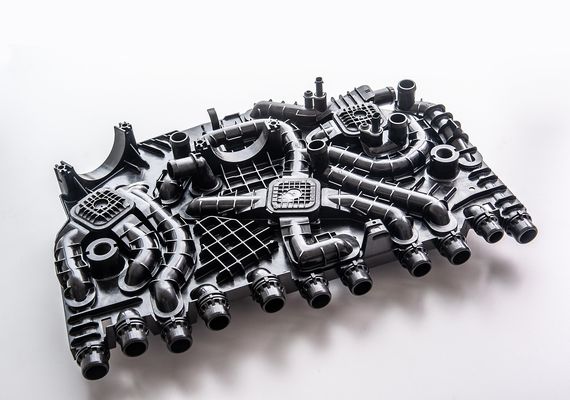
Material challenges and solutions
Developing a material that could withstand extreme temperatures of over 100°C and offer an extended service life was a major challenge. Traditional materials such as PP proved unsuitable due to creep, while PA 6.6 was subject to chemical attack at the weld line. Although PPA and PPS were technically feasible, their higher cost led Sogefi and Porsche to opt for an aliphatic polyketone from AKRO-PLASTIC, AKROTEK® PK VM GF 30 black (8655). Polyketone (PK) also has a significantly smaller ecological footprint, with a CO2 equivalent of 3.08 kg/kg compared to PA 6.6, PPA or PPS. Traditional materials such as PP proved to be inadequate due to creep behavior over the long service life.
Radiator module
The intelligent design and the use of direct welding minimize space restrictions and ensure a compact and efficient system. The use of polyketone (AKROTEK® PK VM GF 30 black (8655)), reinforced by AKRO PLASTIC's innovations, not only extends the life of the module, but also contributes to a reduced environmental impact and expanded manufacturing possibilities. This result represents a significant advance in automotive technology, combining durability, cost efficiency and sustainability.
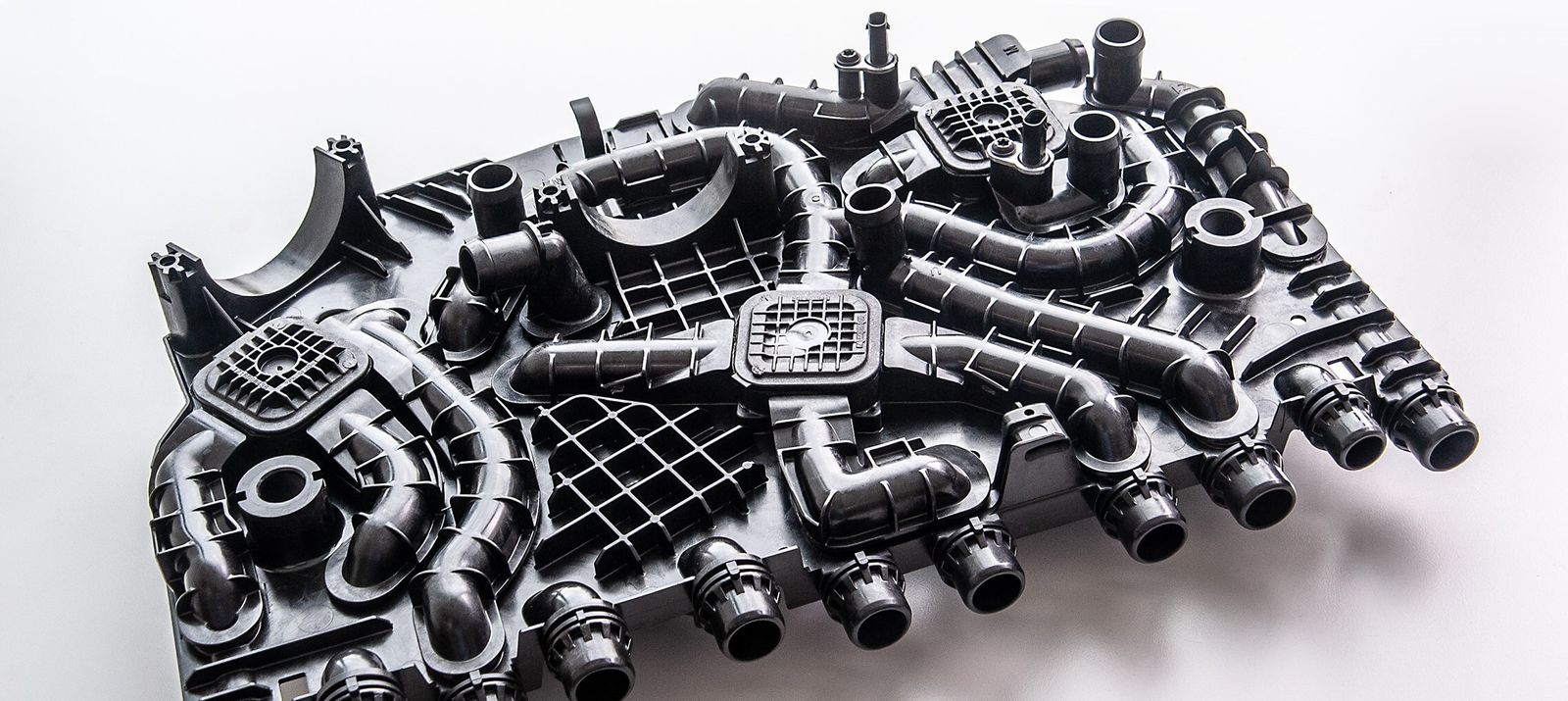
Innovative manufacturing techniques
Given the complex geometry of the components, traditional transition laser welding was impractical. Instead, Sogefi used an internally developed technique of direct laser welding, in which both sides of the weld seam are heated and the parts are joined seamlessly. This innovative method enables precise welding without compromising the dimensions of the components.
To cope with higher laser powers without overheating the surface and risking polymer degradation, AKRO-PLASTIC played a crucial role. They adapted the absorption behaviour and stabilization of the polyketone, AKROTEK® PK VM GF 30 black (8655), significantly extending the process window for direct welding. This breakthrough not only enables efficient production, but also improves the overall performance and durability of the cooling module.