Integrated thermal management module
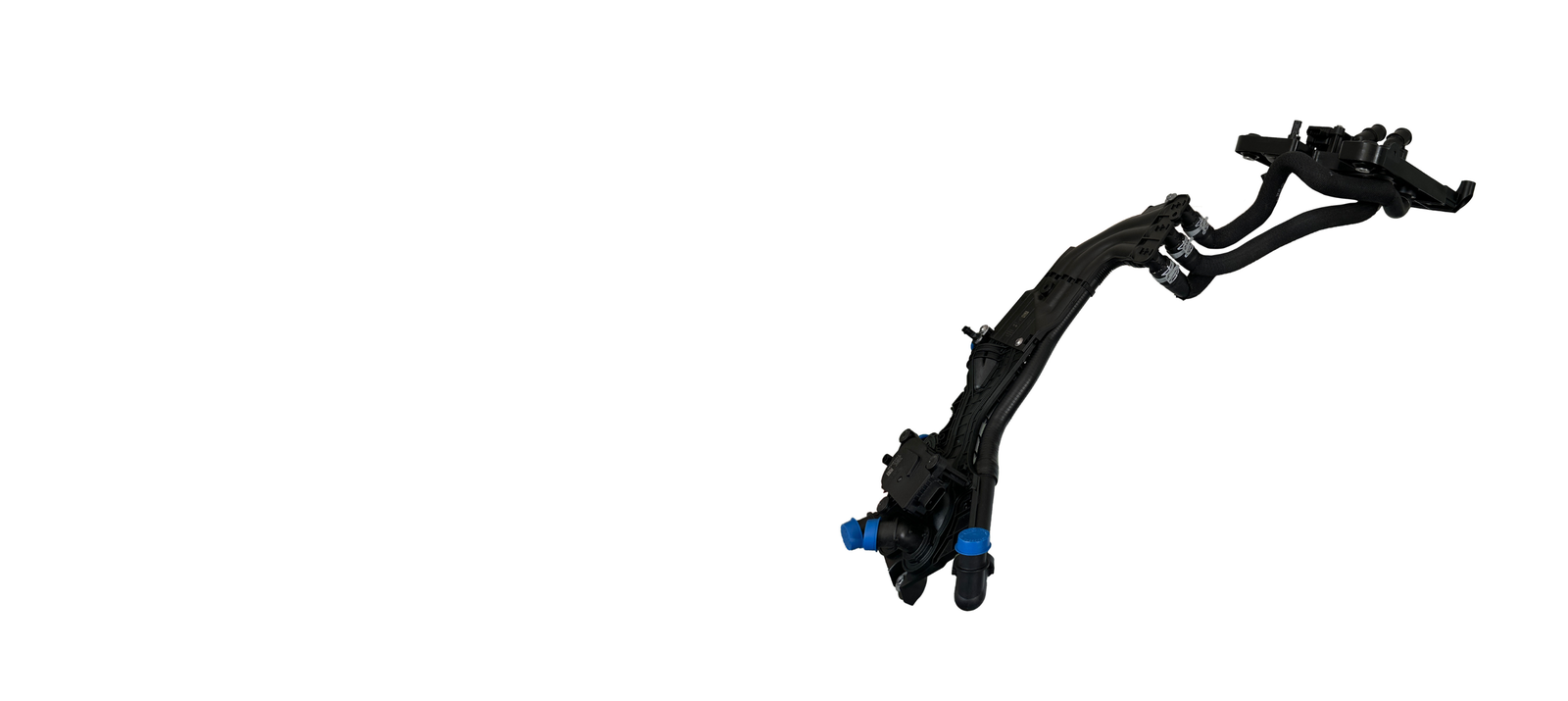
SPE Award 2024 - ‘Nomination Award’ category
Thermal management for electric vehicles
Optimum temperature control of the battery is essential for maximising the performance and range of electric and hybrid vehicles. The target operating temperature of common lithium-ion batteries is around 25 °C. Their service life is maximised at this temperature. In order to reliably guarantee this temperature level, the battery must be cooled or heated depending on external influences.
Requirements for media-carrying systems
The media-carrying systems must be leak-proof and maintenance-free for the entire service life of the vehicle. While combustion engines are usually required to have a service life of 3,000 hours, electric vehicles have requirements of up to 15,000, 30,000 or even 45,000 operating hours. The thermal management system is particularly stressed during fast charging processes.
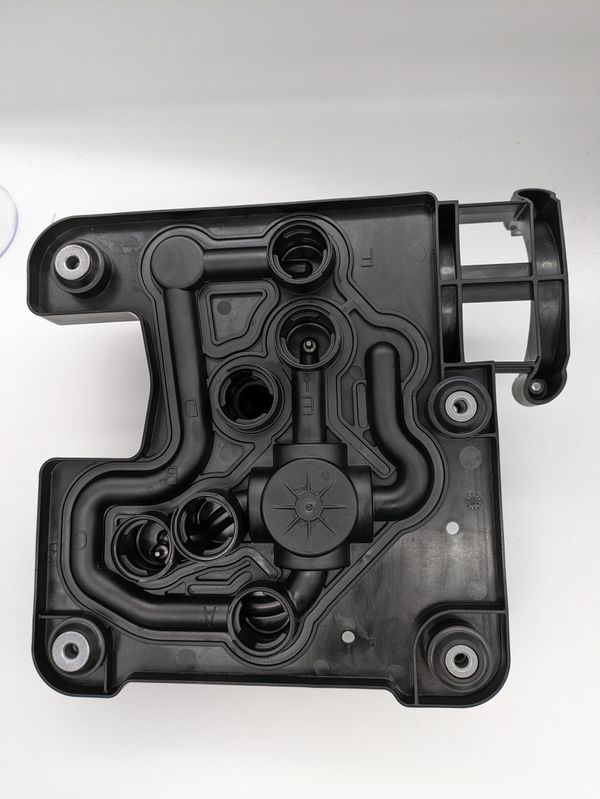
Functionally integrated thermal management module made of polyketone
A functionally integrated thermal management module made of polyketone is manufactured in a double-shell design and joined using laser transmission welding. This is the first application of laser-transparent polyketone in black AKROTEK® PK-VM GF 10 LT black (8290). The tendency of polyketone to cross-link poses a particular challenge during production.
The use of polyketone significantly improves the efficiency and durability of the thermal management systems in electric and hybrid vehicles, which in turn helps to maximise the performance and range of these vehicles.
Materials and their suitability
Polypropylene (PP) cannot meet these requirements in many cases, as component failures occur at 80°C and pressures above 3 bar due to creep behaviour.
Polyamide 66 (PA66) also does not fulfil the requirements due to the long operating times and its rather poor hydrolysis resistance.
With polyketone (AKROTEK® PK-VM GF 10 black (8316), a material was found that offers excellent hydrolysis resistance and very good mechanical properties even at temperatures above 100°C. Polyketone also has cost advantages over PPA and PPS.