Sustainable polyamides
AKROMID® NEXT
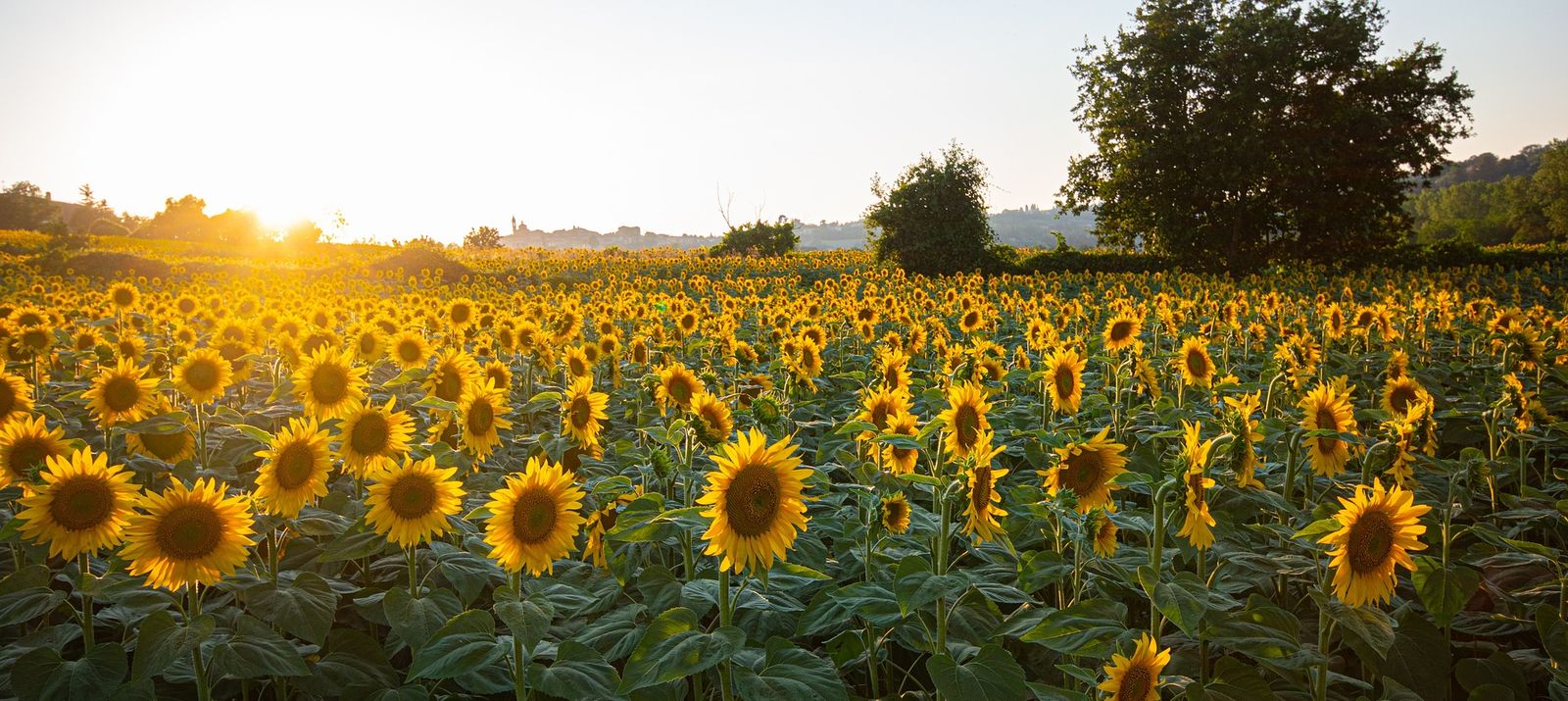
AKROMID® NEXT: PA 6.9, PA 6.10, PA 5.6, PA 11
Overview of sustainable polyamides
With AKROMID® NEXT, we offer innovative and sustainable alternatives to conventional nylons. This new product line has bio-based, biomass balanced or chemically recycled content. Some products are offered with ISCC PLUS or REDcert² sustainability certification.
The majority of polyamides used in plastics processing are produced from fossil raw materials and have a comparatively high CO₂ footprint for polymers. Substitution by polymers with a lower CO₂ footprint, such as polyolefins and polyesters, is not possible in many cases due to the technical properties required.
Polyamides that are fully or partially biobased offer an alternative from the same polymer class and thus comparable material and processing properties. The use of biomass for the production of polyamides reduces dependence on fossil resources as well as greenhouse gas emissions, because plant-based raw materials absorb CO2 from the atmosphere, which is not further emitted at the end of the product life cycle.
AKRO productname | Monomer 1 | Monomer 2 | Raw material | Biobased carbon content | |
---|---|---|---|---|---|
PA 6 | AKROMID® NEXT B | ε-Caprolactam (mass-balanced) | ε-Caprolactam (massebilanziert) | Tall oil | Mass-balanced |
PA 6.6 | AKROMID® NEXT A | Hexamethylendiamine | Adipic acid (mass-balanced) | Tall oil | Mass-balanced |
PA 6.9 | AKROMID® NEXT G | Hexamethylendiamine | Azelaic acid | Sunflower oil | 57 % |
PA 6.10 | AKROMID® NEXT S | Hexamethylendiamine | Sebacic acid | Castor oil | 62 % |
PA 5.6 | AKROMID® NEXT 5.6 | Pentamethylendiamine | Adipic acid | Corn | 41 % |
PA 11 | AKROMID® NEXT U | 11-Aminoundecaoic acid | 11-Aminoundecaoic acid | Castor oil | 92 % |
PP | AKROLEN® NEXT PP | Propylene (mass-balanced) | Propylene (massebilanziert) | Waste oil/Fet | Mass-balanced |
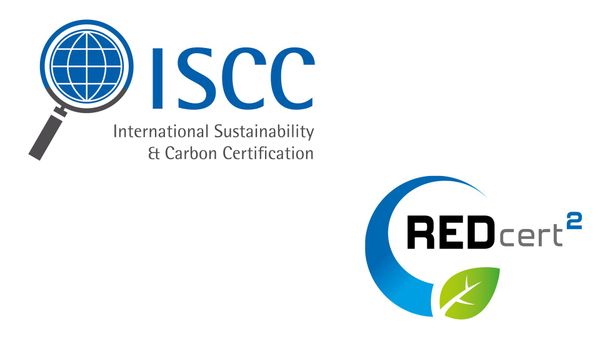
AKROMID® NEXT A and B
In addition to biobased polyamides, compounds made from biomass balanced polyamide 6 or polyamide 6.6 are also available. In contrast to bio-based polymers, finished products are manufactured in the same process as their fossil-based counterparts using the mass balance method. Some of the fossil-based raw materials are replaced by biobased alternatives. A certification process (ISCC PLUS) is used to allocate the biobased raw materials to some of the finished products so that the resulting quality is absolutely identical to the fossil product - but with a significantly reduced carbon footprint.
Biomass-balanced polyamide 6 and polyamide 6.6 can therefore be used as a drop-in solution for the complete variety of existing PA compounds - no new technical qualification or even conversion of the user's processes is necessary. Biomass balanced PA 6 is produced from the biocircular raw material tall oil, a bio-based by-product from the paper industry. Due to the inclusion of biogenic carbon in the LCA balance, the carbon footprint of the polymer is more than halved compared to the European average value for PA 6 of 4.52 kg CO2eq/kg (source: Plastics Europe, 2022).
Show more
In the AKRO-PLASTIC nomenclature, the only change to a biomass-balanced product besides the abbreviation "NEXT" is the term in brackets, which also contains the suffix "BMBCI" (Biomass Balanced Certified ISCC PLUS). The formulation number and all product specifications remain the same as for the fossil variant.
biomass-balanced polyamide 6
AKROMID® NEXT
Under the brand name AKROMID® NEXT, compounds made of biomass-balanced polyamide 6 are available. In contrast to the biobased polymers, the mass balance process produces finished products in the same process as the fossil counterparts. Some of the fossil raw materials are replaced by biobased alternatives. Via a certification process (ISCC PLUS), the biobased raw materials are allocated to part of the finished products, so that the resulting quality is absolutely identical to the fossil product - but with a significantly reduced CO2 footprint.
Biomass-balanced polyamide 6 can therefore be used as a drop-in solution for the complete variety of existing PA6 compounds - no new technical qualification at the user's site is necessary. Biomass-balanced PA6 is produced from the bio-circular raw material tall oil, a by-product from the paper industry. Due to the inclusion of biogenic carbon in the LCA balance, the CO2 footprint of the polymer is more than halved compared to the European average for PA6 of 4.52 kg CO2eq/kg (source: Plastics Europe, 2022).
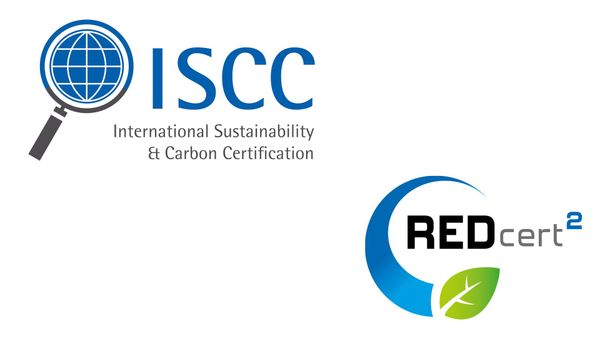
AKROMID® NEXT G, 5.6
AKROMID® NEXT G3 GF 30 1 L CR black (8314) is a glass fibre reinforced PA 6.9/PP blend with biobased content and suitable for weight-reduced, sustainable applications. PA 6.9 is partially biobased (sunflower oil). In addition, the product is certified according to REDcert²: 33 % (allocation factor*) of the fossil raw materials are replaced by sustainably certified, biomass balanced PP.
With AKROMID® NEXT G3 GF 30 1 natural (8085), a non-blended variant with 30% glass fibre is also available. AKROMID® NEXT G is technically suitable to replace PA 6 in many common applications.
The partly biobased AKROMID® NEXT 5.6 3 GF 30 natural (8405) is a HMD-free (hexamethylenediamine) alternative to conventional PA 6.6 compounds with comparable properties. For example, the melting point of 253°C is only about 10°C lower than PA 6.6. PA 5.6 has a lower CO2 footprint and is partly produced from renewable raw materials ( biobased share = 45%*). Increased moisture absorption should be noted. For components with increased impact loads, we also offer AKROMID® NEXT 5.6 3 GF 30 S3 black (8444), a dry impact modified version, also with 30% glass fibre reinforcement.
AKROMID® NEXT
Compound Explorer

Resistance to CaCl2
The PA 6.10 base polymer of AKROMID® NEXT S3 GF 30 1 HU black (8825) is up to 62%² biobased. Due to the longer repeating unit, both PA 6.9 and PA 6.10 have a lower proportion of the characteristic amide groups compared to PA 6 and PA 6.6, which leads to reduced water absorption and increased chemical resistance. The figure shows an example of resistance to CaCl2, which is used for example in road salt to lower the freezing point or as a dust binder for unpaved roads.
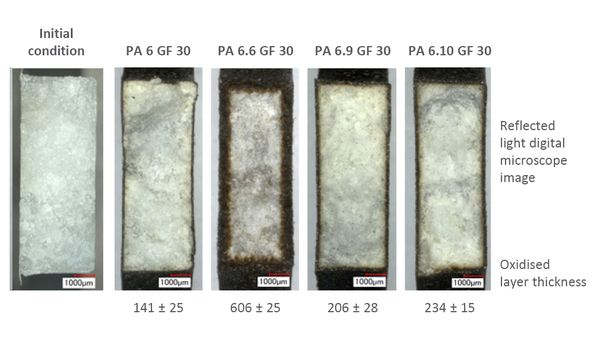
Degree of aging
Hot air storage causes thermooxidative damage to the surface of polyamides, resulting in discoloration and loss of mechanical properties, a process also known as aging. The process occurs primarily at the surface, leaving an undamaged core, as shown in the figure. The thickness of the oxidized layer is a visual measure of the degree of aging.
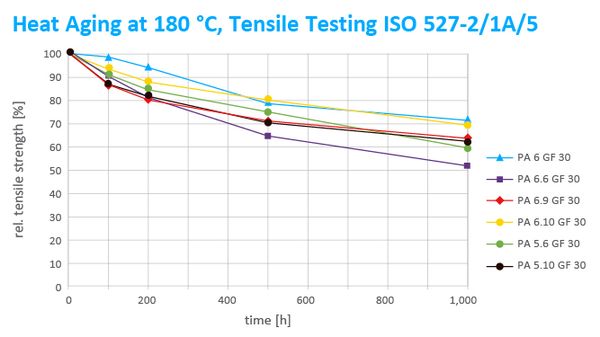
Heat aging test at 180 °C
In the heat aging test at 180 °C, the behavior of the considered biobased polyamides is between PA 6 and the more vulnerable PA 6.6, which can be seen in the drop of tensile strength (see figure).
Of course, AKROMID® NEXT compounds contain a heat stabilization, which strongly improves the aging behavior.
Innovative and sustainable polyamide
AKROMID® NEXT U
AKROMID® NEXT U ICF are carbon fiber reinforced PA 11 compounds that combine performance with sustainability. In addition to the injection molding process, these compounds are also particularly suitable for industrial 3D printing.
The PA 11 is made from castor seed oil (bio-based content > 92%). The carbon fibers are processed from residues of carbon fiber mats (post-industrial recycling content = 100%). In addition, the compounds enable sustainable lightweight construction by combining low density with high rigidity and strength.
Due to the long carbon chain of the monomer, molded parts made from AKROMID® NEXT U have low moisture absorption, which results in high dimensional stability and a low influence of moisture on the mechanical properties. This is a major advantage over molded parts made from conventional polyamides such as PA 6 or PA 6.6.
)
AKROMID® NEXT FR
Recycled materials are often unsuitable as a sustainable source of raw materials, particularly for applications with flame retardant requirements, because the flame retardant properties cannot be reliably achieved due to impurities or fluctuations in the starting material. It therefore makes sense to use bio-based variants for these products in particular in order to reduce the CO2 footprint, as they are characterized by controlled virgin material quality.
All flame retardant compounds based on PA6 and PA6.6 are also available as biomass-balanced variants, which not only use mass-balanced polymer raw materials, but also a certified sustainable flame retardant that is also free from halogens, antimony trioxide and red phosphorus.
Bio-based polyamides with a flame retardant finish are also available. AKROMID® NEXT 5.6 3 GF 35 9 FR natur (8401) achieves UL94 V0 classification at 1.6 mm and is suitable for components with high strength requirements for the E&E market and e-mobility. It is an HMD-free (hexamethylenediamine) alternative to PA 6.6 with comparable properties. The partially bio-based PA 6.9 with the name AKROMID® NEXT G3 K8 9 FR LA weiß (8261) complies with UL94 V2 and GWFI 960 °C and retains a high CTI of 600 V. The material is 20 % glass fiber reinforced and can be laser-marked with a dark color change, which fits well with the requirements of the E&E market, e.g. for terminal blocks.
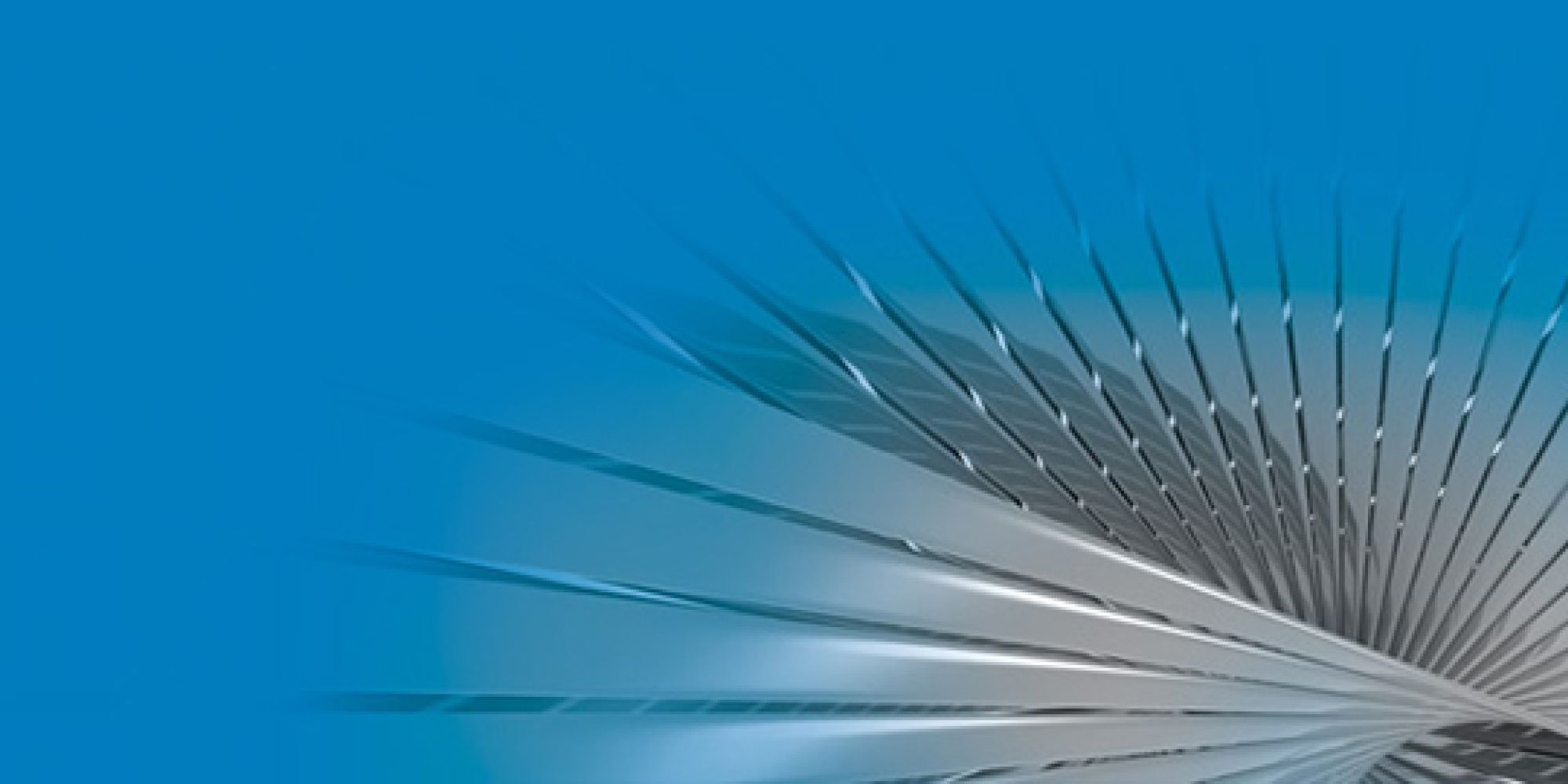
Productinfo
AKROMID® NEXT Compounds
Here you will find information that applies to all products of the AKROMID® NEXT series
Sustainable plastic compounds
Do you have questions to our sustainability certifications?
Arrange a personal online appointment with one of our experts. Find out what we can do for you in a personal one-on-one meeting. Completely free of charge and without obligation.
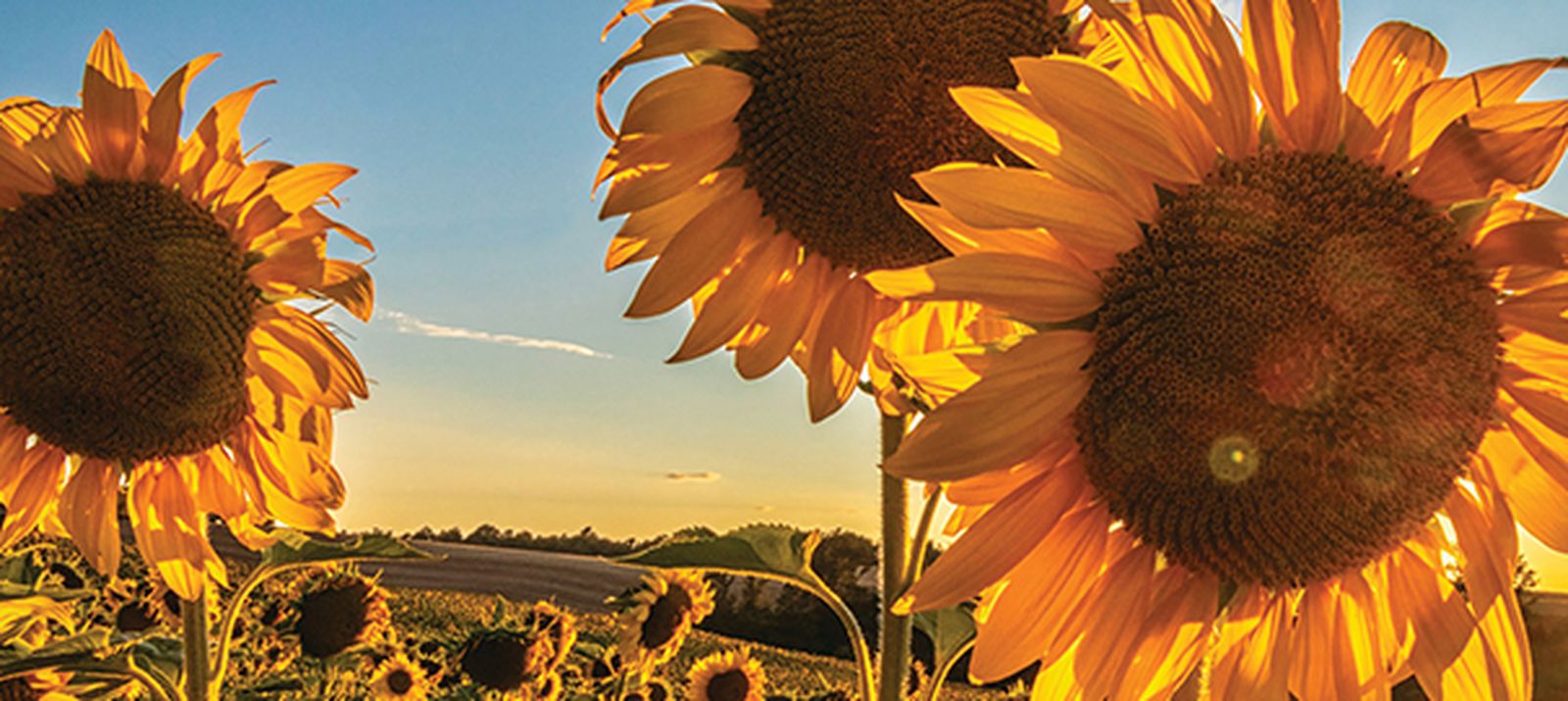
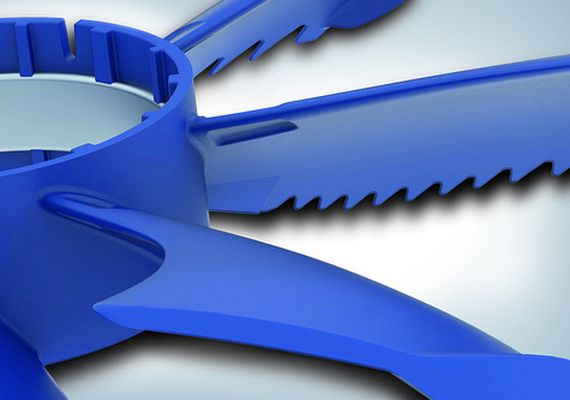
NEWS Interplay of design + material
The application of bionic bio-fan made of the PA-6.10 compound AKROMID® S convinces by a high biogenic C content. In addition, the component weight was reduced and a high dimensional consistency was achieved with our material. Learn more about the project in our Sucess story.
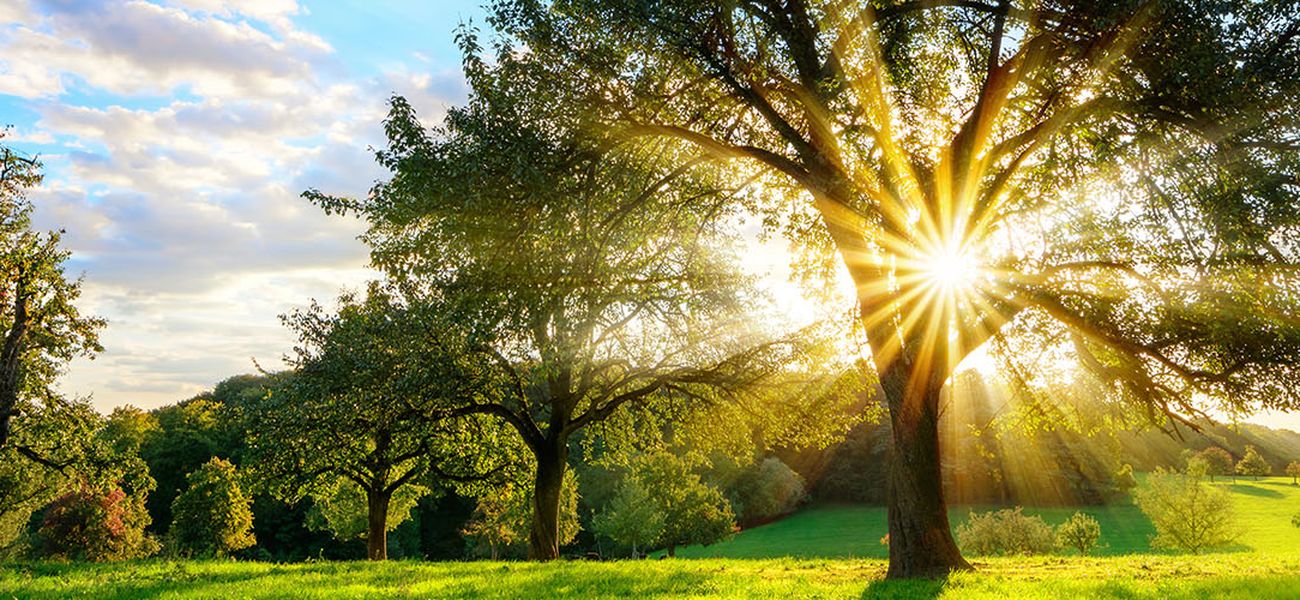
Disclaimer: All specifications and information given on this website are based on our current knowledge and experience. A legally binding promise of certain characteristics or suitability for a concrete individual case cannot be derived from this information. The information supplied here is not intended to release processors and users from the responsibility of carrying out their own tests and inspections in each concrete individual case. AKROMID®, AKROLEN®, AKROLOY®, AKROTEK®, ICX®, PRECITE® and DIA(hr)LOG® are registered trademarks of AKRO-PLASTIC GmbH.