Sustainability lexicon
Frequently asked questions about sustainability
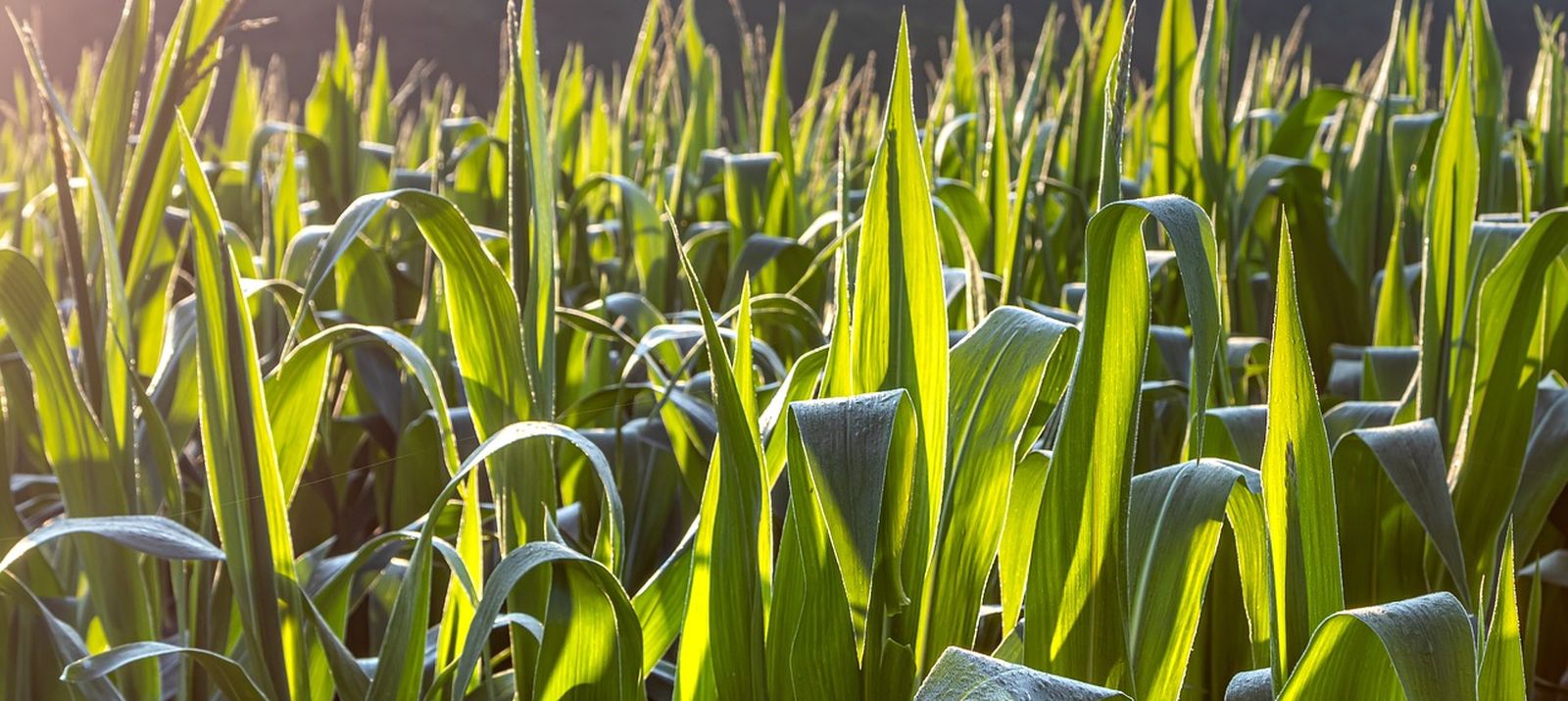
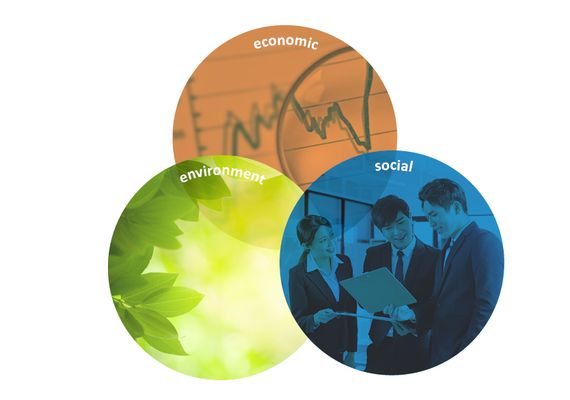
Sustainability
In the past: Sustainability means to cut only as much forest as will grow back again. (Definition according to Hans Carl von Carlowitz, 1713)
Today: The goal is to leave an intact world to future generations through economical, responsible use of the available global resources (e.g. oil, fish and forest stocks, CO2 budget, etc.). To achieve this, social, ecological and economic aspects must be given equal attention.
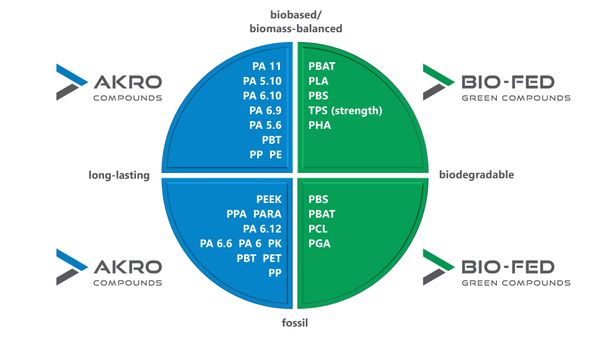
Biopolymers
Biopolymers can be divided into three categories:
Biobased polymers that are not biodegradable ► AKRO-PLASTIC
Biopolymers that are petrochemically produced but biodegradable ► BIO-FED
Biobased polymers that are biodegradable ► BIO-FED
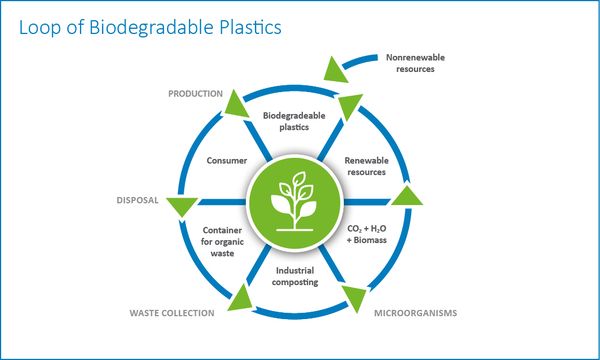
Biodegradable Polymers
Biodegradable polymers can be converted into CO2, water and biomass by microorganisms (e.g. fungi or bacteria). This depends only on their chemical structure, but not on the feedstock (biobased or fossil). Biodegradability is strongly influenced by the environment: temperature, type of microorganisms, duration of exposure, aerobic/anaerobic. There are different standards, labels and certification systems for different environmental conditions (e.g. industrial compost, home compost, agricultural soil, ocean). Biodegradable polymers are mostly used for short-lived consumer products or for products that are likely to end up in nature.

Biomass
Biomass is a material from biological sources, e.g. agricultural plants, trees, seaweed or microorganisms. It therefore does not come from fossil or geological sources (e.g. petroleum or stone).
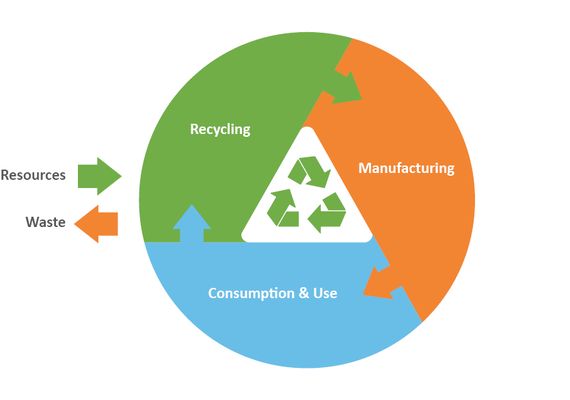
Circular Economy
The Circular Economy is about reducing waste and reusing materials. For example, waste from industry or consumers is reprocessed (recycled) to make new products. A typical example is the collection of PET deposit bottles, which are reprocessed into plastic pellets. The Circular Economy is considered sustainable by
the avoidance/reduction of waste
the saving of fossil resources
the potential to reduce greenhouse gases (GHG):
In general, the mechanical recycling of plastics causes less GHG emissions than the production of a virgin plastic. This is due, among other things, to lower energy consumption and the shorter process chains.
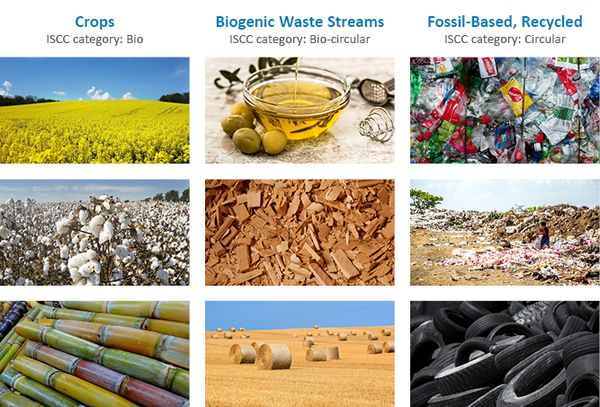
Bio, Bio-Circular and Circular
The terms come from the ISCC PLUS certification. They denote different categories of raw materials:
Organic: Material that uses virgin agricultural raw materials (e.g. sugar cane, corn, etc.) at the beginning of the value chain
Bio-Circular: Material that uses bio-based waste materials (e.g., grease and oil waste) at the beginning of the value chain
Circular: Material that uses recycled, fossil-based raw materials (e.g., recycled plastic) at the beginning of the value chain
Definition SDGs
Sustainable Development Goals
The United Nations adopted the 2030 Agenda on September 25, 2015, which includes 17 Sustainable Development Goals (SDGs) to be achieved by all UN member states between 2016 and 2030. The Sustainable Development Goals represent a global plan to promote sustainable prosperity and peace and to protect our planet.
As a manufacturing company and member of a successful, globally active group of companies, AKRO-PLASTIC sees it as its duty to contribute to the fulfillment of these goals.
Definition: Biobased Polyamides
Biobased Polyamides
For long-term applications, e.g. in the automotive, construction and electrical and electronics sectors, bio-based engineering plastics that are not biodegradable are suitable. These include biobased polyamides. The oldest bio-based polyamides are PA 11 and PA 6.10, which are based on castor oil. In the meantime, the range of industrially produced biobased polyamides has expanded significantly, including PA 6.9, PA 5.6 and PA 5.10.
Definition: Bioeconomy
Bioeconomy
In the bioeconomy, renewable, biological raw materials (biomass) are used to produce value-added products. These include food and feed, biobased consumer products, or bioenergy. For consumer products made from biomass, the following sustainable benefits arise:
Reduces the dependence on fossil, limited resources
Potential to reduce carbon dioxide (CO2) emissions
Plants absorb CO2 from the atmosphere as they grow and convert it to biomass. At the end of life of a 100% biobased product, these CO2emissions are released (e.g. through waste incineration), which were previously removed from the atmosphere. In contrast, petroleum serves as a feedstock for fossil-based materials. Crude oil, which is already many millions of years old, is extracted from the depths of the earth and has bound a large amount of CO2 in the form of hydrocarbon chains. So at the end of life of fossil-based products, additional CO2 emissions are released into the atmosphere, adding to the climate crisis.
The carbon footprint of biobased products is therefore reduced by the stored biogenic carbon of the product. As a result, the carbon footprint can be lower than the value of the fossil-based variant.
Definition: CFP
Carbon footprint of Products
The carbon footprint of products (abbreviated CFP) indicates how much greenhouse gas emissions (GHG) are caused in total by a specific product (goods or services). It therefore describes the impact on the climate crisis. As a synonym, the term CO2 footprint is also used in Germany. Different life cycle phases can be considered, e.g. cradle-to-gate or cradle-to-grave.
A cradle-to-gate approach is also referred to as a partial CFP, since the balance does not take the entire life cycle into account, as is the case with the cradle-to-grave approach. The CFP is given in CO2 equivalents and is always related to a specific functional unit, in the case of our products kgCO2eq per kg of compounded plastic granulate.
For the balancing of the CFP there are different standards, among others the ISO 14067, GHG protocol or PAS 2050.
AKRO-PLASTIC is able to show the Carbon Footprint for the majority of all products. For this purpose, we will gladly provide you with a Carbon Footprint Report, which is always accompanied by a letter informing about the calculation methodology and the data basis. Please ask your responsible customer contact.
Definition: Life cycle assessment
Life Cycle Assessment (LCA)
A life cycle assessment involves considering a variety of environmental impacts of a product. These environmental impacts may include: Acidification of soils, toxicity to humans, depletion of the ozone layer, land, water and resource consumption. A life cycle assessment typically includes a climate impact assessment, or carbon footprint. Well-known standards for balancing are, for example, the ISO standards 14040/14044.
The environmental impact of a product can be assessed with the help of the LCA. The CFP alone is less suitable for this purpose, as it only describes one environmental impact, albeit the most important one at present. At the same time, the LCA is significantly more costly and complex than the balancing of a CFP.
Definition: ISCC PLUS and REDcert²
ISCC PLUS and REDcert²
Two leading certification systems for sustainable materials in the chemical industry. Biomass and fossil-based recyclates are used as raw material sources to produce biomass-balanced or recycled-mass-balanced products. Among other things, fossil resources are saved and attention is paid to ecologically and socially sustainable aspects when growing the biomass. More detailed information can be found here: ISCC PLUS and REDcert²
Definition: Mass balance approach
Mass Balance Approach
A method to track and certify in a simple way the material flow of biomass/recycled material. It is used within sustainability certification schemes, such as ISCC PLUS and REDcert². More detailed information can be found here: ISCC PLUS and REDcert²
Definition: Allocation factor
Allocation Factor
The value chain of products in the chemical industry is often very complex. In order to be able to track the sustainable material flow in a simple way, the mass balance approach is used.
We use the allocation factor to show how much biomass and / or recycled material is allocated to the certified product. The allocation factor indicates the proportion of fossil resources that have been replaced by biomass and / or recyclate in the value chain of the material. It is given as a percentage (max. 100%) and refers to the organic share of the product. The correctness of the allocation is confirmed by ISCC PLUS or REDcert² certification.
The principle behind this is the same as for green electricity: The consumer does not know whether the electricity from his socket is generated directly from renewable energies. However, the electricity provider is obliged to feed the corresponding amount into the power grid. Overall, this increases the amount of green electricity. Similarly, the use of sustainable materials is increasing in the chemical industry. The following graphic illustrates the mass balance approach.
Definition: Biomass balanced and recycling mass balanced
Biomass balanced and recycling mass balanced
ISCC PLUS or REDcert² certified materials are mass balanced materials. This means they save fossil raw materials by using sustainable raw materials in the value chain.
The term biomass balanced refers to the use of biomass at the beginning of the value chain. Similarly, recycled-mass-balanced materials use recycled, fossil-based raw material sources.
Definition: Recyclate
Recyclate
AKRO-PLASTIC defines all raw materials as recycled material according to the standard DIN EN ISO 14021. According to this, recyclate is a recycled material, which has been processed from waste to an (intermediate) product. A distinction is made between post-industrial and post-consumer waste:
Post-Industrial (PIR) = waste before use, i.e., separated from the waste stream during the manufacturing process, e.g., start-up lumps, sprues. This does not include the reuse of scrap materials that are reused in the same process.
Post-consumer (PCR) = waste after use, i.e. it concerns materials from end consumers, e.g. from households, which can no longer be used for the intended purpose (example: packaging).
AKRO-PLASTIC uses the following recyclates:
Recycled carbon fibers (ICF)
Polyamide recyclates
Glass beads
PET bottles
Definition: Chemical recycling
Chemical recycling
In chemical recycling, unlike mechanical recycling, the polymer structure is not retained. The polymer macromolecules are broken down back into smaller molecules such as monomers, oligomers and other hydrocarbons. New polymer can then be produced again from the raw materials produced. The main advantage of chemical recycling is therefore that the quality of a chemical recyclate is equivalent to a virgin material.
Definition: Pyrolysis
Pyrolysis
In pyrolysis, the plastic is heated to approx. 650°C in an oven in the absence of oxygen. Without the oxygen, the plastic does not burn and no CO2 is produced. Instead, the polymer gradually decomposes into smaller molecules. Polymers are particularly suitable for pyrolysis in this case, but so are other hydrocarbon-containing wastes such as old car tires. It is also possible to process mixed plastic waste if existing pollutants are subsequently removed from the product. The pyrolysis oil obtained from the process is recycled at the beginning of the chemical process - in the steam cracker - and thus becomes a raw material for many chemical products, including monomer or polymer production. AKRO-PLASTIC will soon offer chemically recycled polyamide from pyrolysis. Stay tuned!
Proof of the use of raw materials from pyrolysis is provided by the mass balance approach. The products are offered either according to the ISCC PLUS certification procedure or REDcert². Analogous to biomass-balanced products, the polymer also comes from the same process or the same factory as the corresponding fossil polymer, so there are no quality losses or differences. Polyamide 6 or 66 from chemical recycling can therefore be used as a drop-in solution for existing compounds - unlike biobased polyamides with a different polymer structure, a renewed technical qualification at the user is not necessary.
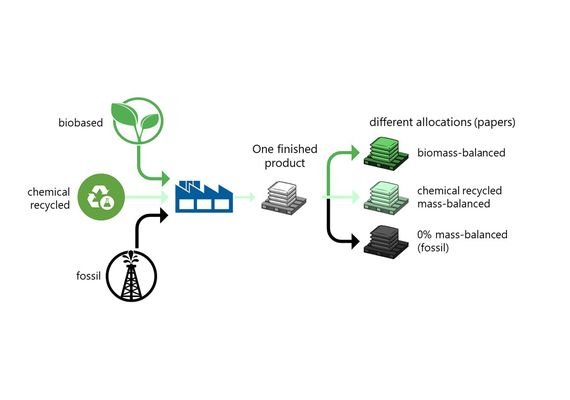
Production steps
Because all production steps from normal plastics production are run through again during pyrolysis, the CO2 footprint of chemical recyclate from pyrolysis hardly differs from virgin material. However, the process can make an important contribution to saving fossil raw materials.
Solvolysis
In solvolysis, polymers are split into monomers under the action of solvents. This is a very selective process, which is why the process has to be adapted individually to each polymer. As a result, only previously sorted waste streams can be processed. The process is mainly used for processing polycondensates (PET, PA6, ...), as well as polymers with N or O in the main chain.
In the case of polyamide 6, despite intensive research, the process is not commercially available at present. However, the potential of solvolysis is great, especially with regard to sustainability: the process allows the monomer ε-caprolactam to be produced directly and returned to polycondensation without further intermediate steps. This eliminates the actual monomer production, which normally causes the largest share of the CO2 footprint in the value chain.