Foaming
Lighter than water
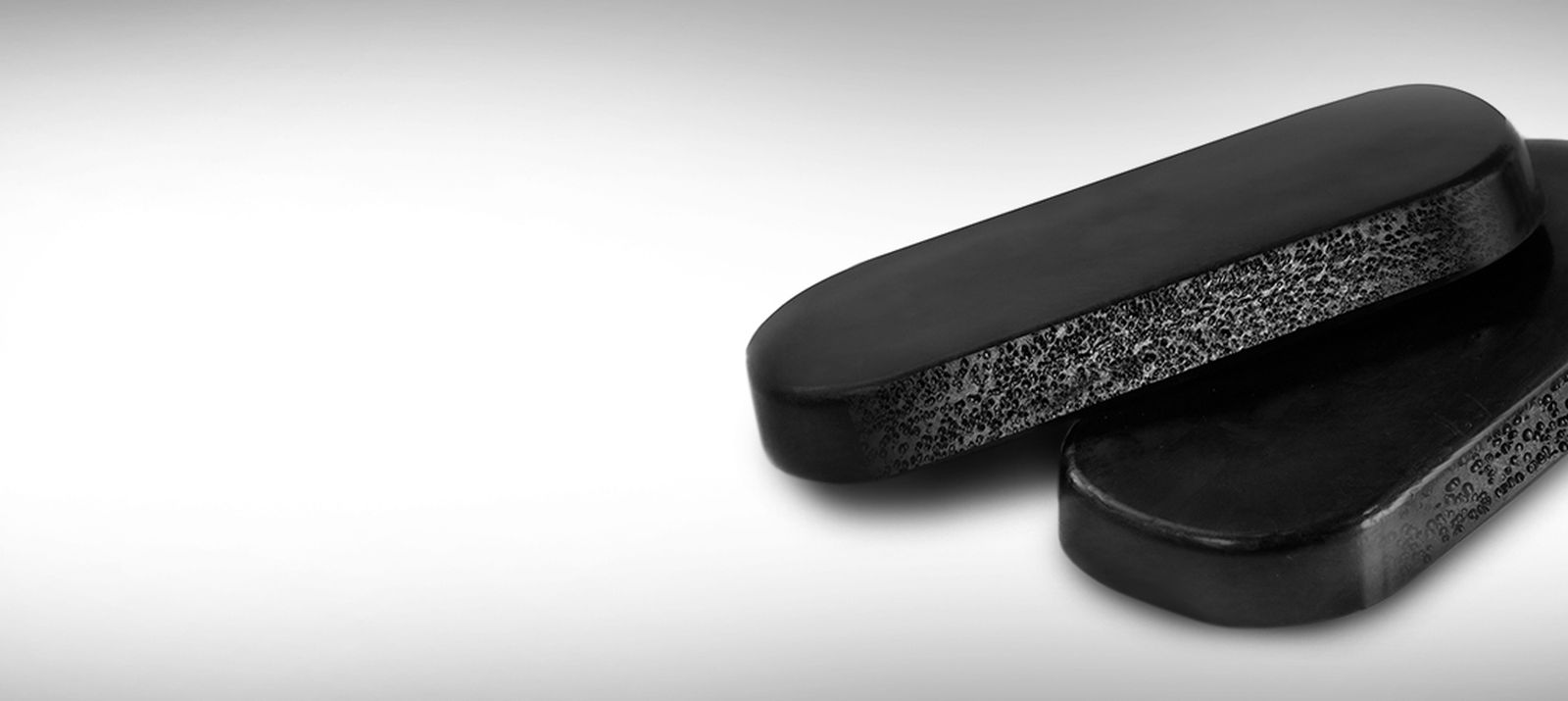
Lighter through Foaming
Motivation for foaming of thermoplastic polymers
Thermoplastic polymers can be foamed physically or chemically. Although most of the time, this technology is used to achieve weight reductions in the component, there are multiple advantages:
Weight reduction / material savings
Reduction of CO2-Emissions
Reduction of sink marks
Reduction of warpage
Realization of parts with greater wall thicknesses
Increase of the stiffness-to-weight ratio
Foaming Processes
AF-Complex® TM
The production of micro-cellular foams by means of chemical or physical methods is one of the most important developments in plastics processing technology.
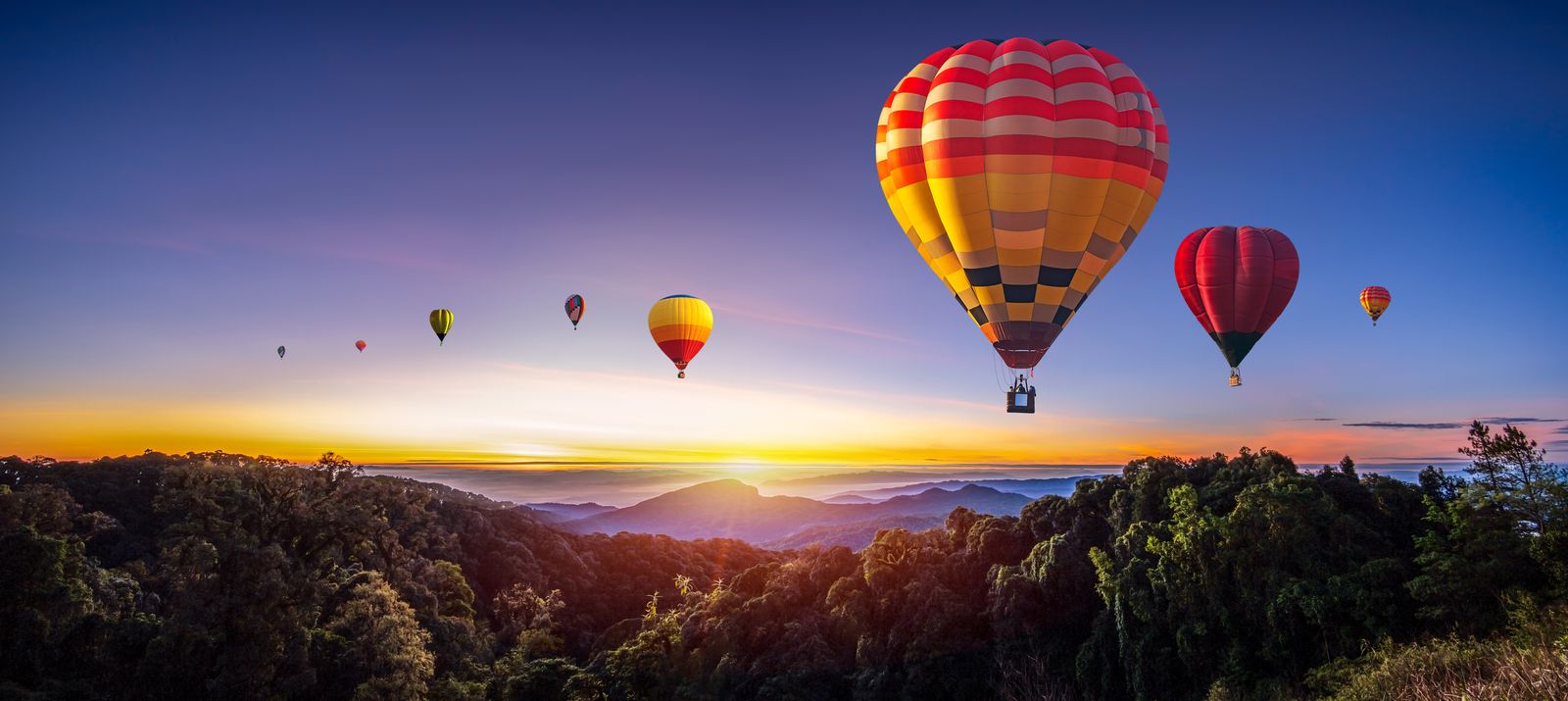
Process Variations
Process variant of thermoplastic foam injection molding
Core-Back Injection Molding
Core-Back Injection Molding is a process variant of thermoplastic foam injection molding which can be combined with chemical or physical foaming agents. In this process, foaming of the thermoplastic melt is achieved by increasing the base wall thickness of the component.
The process begins after the cavity has been filled completely (full shot). After a short delay time when a compact boundary layer has formed, the mold opens by means of precision opening until the desired opening stroke has been reached. During the opening, a pressure drop takes place in the cavity and the gas can escape from the plastic melt and thus expand. Due to the defined mold opening, the plastic does not lose contact with the mold wall during expansion, allowing the foam structure to form inside. The foaming process causes the wall thickness of the component to increase continuously during the opening until the desired opening stroke is reached. This is followed by the standard residual cooling time. Subsequently, the mold opens, and the component is demolded.
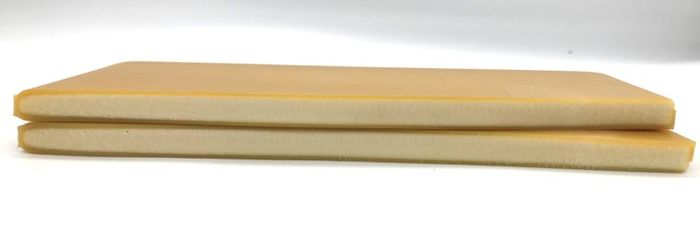
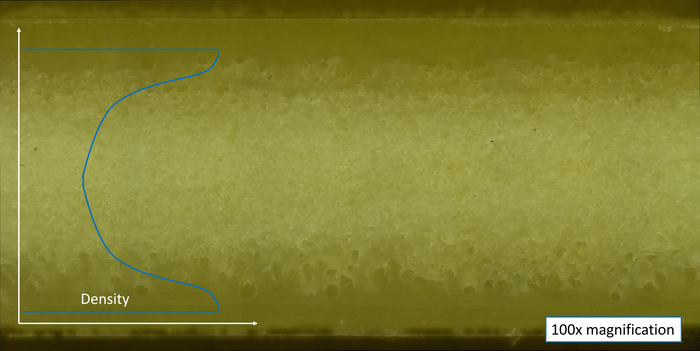
Integral foams are produced in the Core-Back Injection Molding process. These are characterized by a compact, solid skin layer followed by a porous, flexible foam structure inside the component. The density of the material thus decreases continuously from the outside to the inside. For this reason, the process is used primarily in the field of lightweight construction, e.g., for beams, underbody panels, etc. In this area, it can provide high cycle time reductions as well as weight savings in the order of 30 % and more. However, it requires a holistic approach - design / material / manufacturing technology - and requires additional machine equipment (precision control for the clamping unit). (Reference: thermoPre symposium 2019 "From fiber to component").
Technical center of AKRO-PLASTIC
A 300 t ENGEL victory injection molding machine in the technical center of AKRO-PLASTIC is equipped with a precision opening control system. So far, we have successfully sampled different components using this process. In a cooperation with the company Arburg, for example, we were able to produce demonstrator components with integral foams, which have both a good foam structure and surface quality with weight reductions of 55 - 60 %.
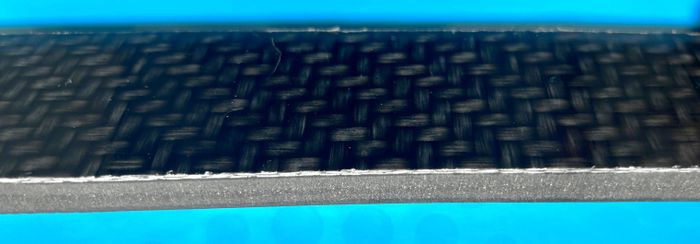
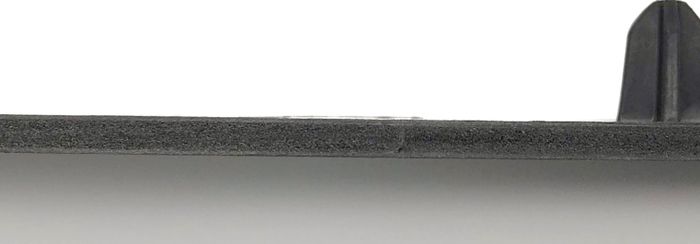
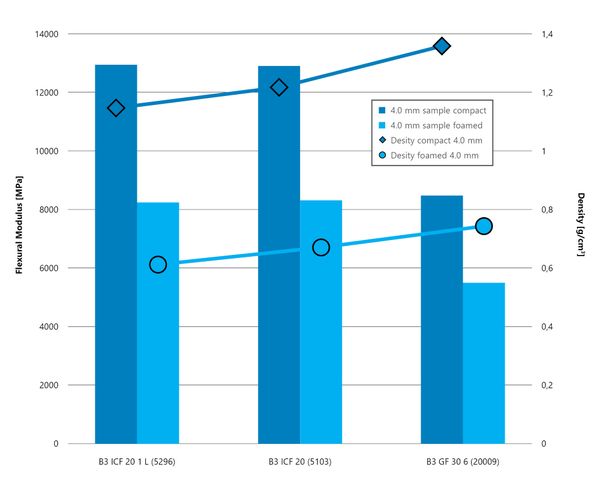
Weight reduction in core back injection moulding
Wall thickness of the part stays the same
45 % weight reduction yields only 35 % reduction in flexural stiffness
Absolute density of foamed AKROMID® B3 ICF 20 (5103): 0,67 g/cm3 with a flexural modulus of 8400 MPa
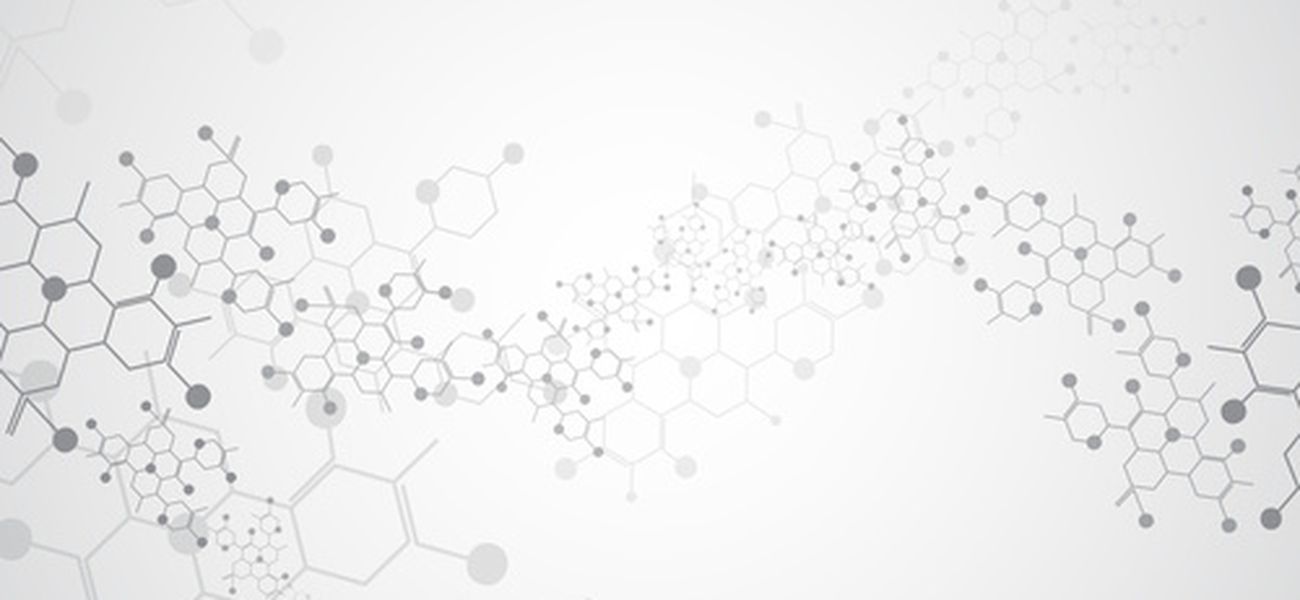
Download
Lighter than water
We achieve the best values of weight-specific mechanics by using our ICF polymers for foaming!
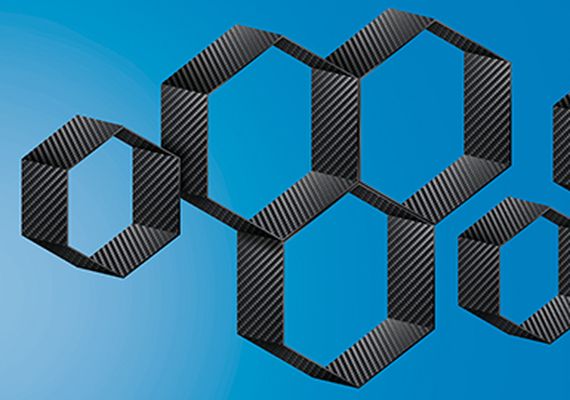
The lightest polymers of AKRO-PLASTIC
AKRO-PLASTIC has developed new ways to incorporate dry, conditioned carbon-fiber fabrics into a polymer melt in a manner which enhances the added value.
This involves shredding the fabrics in a multiple-step process so that they can be gravimetrically dosed on an extruder, like conventional cut-carbon fibers.
Tensile testing shows that even at higher temperatures, approximately the same strengths can be achieved with lighter ICF compounds from AKRO-PLASTIC than with significantly higher glass-fiber reinforcement content.
Show more
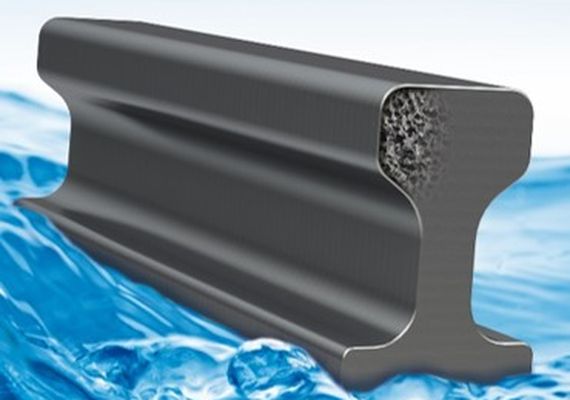
Thermoplastic Polymers
In its search for weight-saving potentials, the plastics industry is continuously finding new solutions. By adding a chemically coupled polypropylene, and after moisture absorption, a newly developed polyamide blend (PA+PP) from AKRO-PLASTIC GmbH in Niederzissen, Germany, exhibits the same strength as a standard polyamide. Depending on application and the degree of reinforcement, the blends already save 7-10 % of density compared with standard polyamides, and have a better flowability. In order to reduce component weight even more, one approach is to charge the melt with a chemical or physical foaming agent.
Talk to Our Experts
With a worldwide network of plastics distribution experts, we can provide you with support anywhere in the world. Talk to one of our specialists to find out more.
