Carbon fibre reinforced compounds
)
ICF-COMPOUNDS
Lightness, structure, stiffness and a competitive edge, all combined in a single material
As Henry Ford put it, “You can have any color, as long as it’s black”. The same is true for ICF products from AKRO-PLASTIC GmbH, as they also come only in black. What makes our innovative, carbon fibre-based compounds stand out is their extreme stiffness and extremely competitive price tag.
Using proven compounding technology from our sister company, FEDDEM GmbH & Co. KG, we offer ICF compounds based on polyamide 6 (AKROMID® B), polyamide 6.6 (AKROMID® A), PPA (AKROMID® T), PA 6.6 with a partially aromatic CoPA (AKROLOY® PA) or PARA based (AKROLOY® PARA) as well as an aliphatic polyketone (AKROTEK® PK) and polyster (PRECITE®). The compounds are finished with a carbon fibre content of 10 % to 40 %.
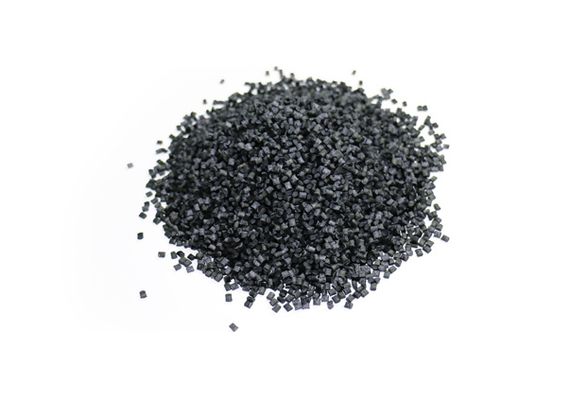
• Good tribological properties (low-wear)
• Good electrical conductivity
• Good thermal conductivity
• Excellent stiffness and flexural stiffness
• Good flexural stress
• Low linear thermal expansion
Sustainable Alternatives
To improve the products Co² footprint we can also offer our new AKROMID® NEXT product line with a sustainable alternative.
AKROMID® NEXT G3 ICF 15 7 L CI black (8379) is combining low density polymer matrix with low density reinforcement. This PA 6.9/PP blend with 15 % recycled carbon fibre is also made from bio-based and bio-mass balanced polymers. This product can be officially certified by ISCC PLUS or REDcert².
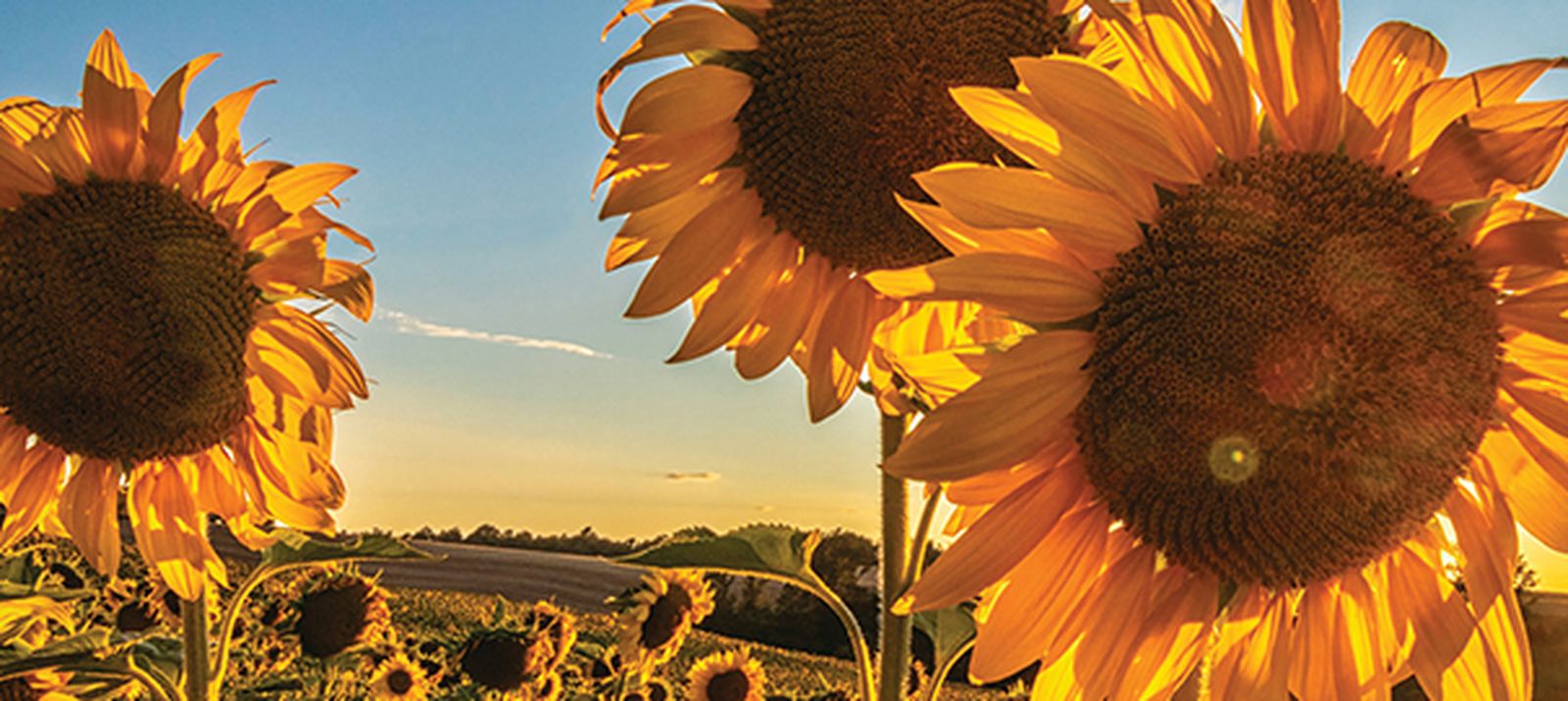
ICF-Compounds
Production process for ICF Compounds
AKRO-PLASTIC has developed new ways to incorporate dry, conditioned carbon fibre fabrics into a polymer melt in a manner which enhances the added value. This involves shredding the fabrics in a multiple-step process in such a way that they can be gravimetrically dosed on an extruder, like conventional cut-carbon fibres. The biggest obstacle in this process is a powder binder applied to the fabric. The powder binder is used to superimpose several layers of the carbon fibre fabrics and prevent slippage in subsequent processes. An important step during the conditioning of the fibres is the dosing of the fabrics, which can only be ensured with precise temperature control.
The synchronous twin-screw extruder used at FEDDEM GmbH & Co. KG has been equipped with a newly developed side feeder. Depending on the polymer, this side feeder is capable of gently delivering up to 40 % carbon fibre content to the conditioned polymer melts. A further critical step when incorporating the prepared carbon fibres is the proper electrical encapsulation of the system technology and suitable extraction of the dosing. Otherwise, the high conductivity of carbon fibres will relatively quickly result in the destruction of the contaminated electrical components.
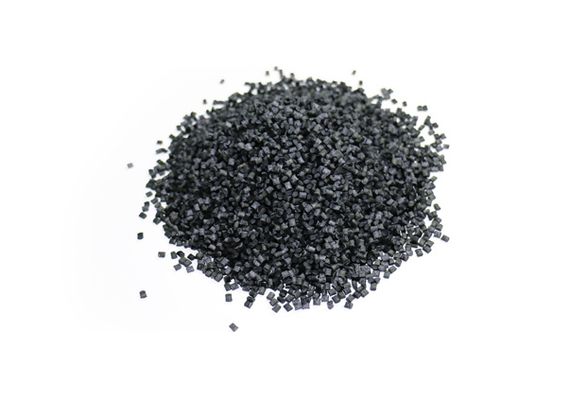
Advantages of ICF Compounds
Tensile testing shows that even at higher temperatures, approximately the same strengths can be achieved with lighter ICF compounds from AKRO-PLASTIC than with significantly higher glass fibre reinforcement. The elongation at break for carbon fibre reinforced compounds, however, is slightly less than for compounds with glass fibre reinforcement.
Compared with glass fibres, the use of carbon fibres gives rise to an extreme increase in stiffness in thermoplastic compounds. This becomes clear when looking at the specific tensile modulus, that is, the tensile modulus divided by density. The ICF compounds from AKRO-PLASTIC dominate, particularly when freshly moulded. But even for conditioned compounds, the specific tensile modulus for all compounds is higher than that of a glass fibre reinforced alternative compound.
The AKROMID® Lite compounds do particularly well in this comparison. In this respect, the specific stiffness of a conditioned AKROMID® B3 ICF 20 1 L is approximately as high as that of a freshly moulded AKROMID® B3 GF 40 1 L.
This means that given identical geometry, components can be realised in practical applications with comparable or even greater stiffness and lower weight. For dynamically loaded structural components, the part design can be adapted based on the gain in stiffness, thereby adding to the weight savings.
)
ICF Clutch Pedal
The aim of the new product line is to massively reduce the weight of high-strength components. As the price is now approaching that of glass fiber compounds for the first time, nothing stands in the way of substitution from an economic point of view. The fact that a clutch pedal can be stably manufactured in such a sensitive process as the internal water pressure process shows how high the quality of the newly created product range is.
Together with the companies Engel, PME Fluidtec and Moldetipo, we have succeeded in reducing the weight of the component by 10% while achieving improved mechanical values.
The advantage of carbon fiber-reinforced compounds can also be used in many other applications, especially in load-bearing components. In applications such as center consoles, activated carbon filters or brackets for control units, other benefits of carbon fiber could also be useful. These include: electrical shielding, good thermal conductivity and a lower coefficient of thermal expansion.
Properties | Test method | B3 GF 30 GIT black(4599) | B3 ICF 15 black (5026) |
---|---|---|---|
Compound density | ISO 1183 | 1,36 g/m³ | 1,18 g/m³ |
Component stiffness | 100 % | 125 % | |
Component breaking force | 999 +/-40 N | 1.100 +/-15 N | |
Component weight | 319 g | 291 g |

Weight Reduction
New blowing agent systems result in weight reduction in engineering plastics, with optimal retention of the mechanical properties and surface qualities. These blowing agent masterbatches combine the advantages of dust-free, safe handling whilst providing nucleating agents and additives which can enable in-process realisation of an optimally fine-tuned product.
In process control there are two different approaches, which are compared in the table below using dumbbell specimens in a 20 % carbon fibre reinforced (PA + PP) blend, loaded with 3.5 % masterbatch AF-Complex® PE 990310 TM. The respective compound, loaded with blowing agent and produced in a standard process, serves as the zero value. Moisture absorption influences the variants thus foamed to the same degree as the non-foamed variants.
Show more
Properties | Unit | AKROMID® B3 ICF 20 1 L | AKROMID® B3 ICF 20 1 L | AKROMID® B3 ICF 20 1 L |
---|---|---|---|---|
Shot method | Zero value | Short shot | Full shot | |
Holding pressure | without holding pressure | without holding pressure | without holding pressure | |
Partial fill | Partial fill | |||
Blowing agent | % | 3,5 AF-Complex® TM | 3,5 AF-Complex® TM | 3,5 AF-Complex® TM |
Tensile modulus | MPa | 12.510 [100%] | 10.660 [85%] | 12.200 [97%] |
Flexural modulus | MPa | 12.100 [100%] | 12.240 [101%] | 12.260 [101%] |
Flexural strength | Mpa | 202 [100%] | 185 [92%] | 198 [98%] |
Flexural strain | % | 2,7 | 2,4 | 2,6 |
Weight reduction | % | 13 | 4 | |
Density | g/cm³ | 1,10 | 0,96 | 1,06 |
Applications
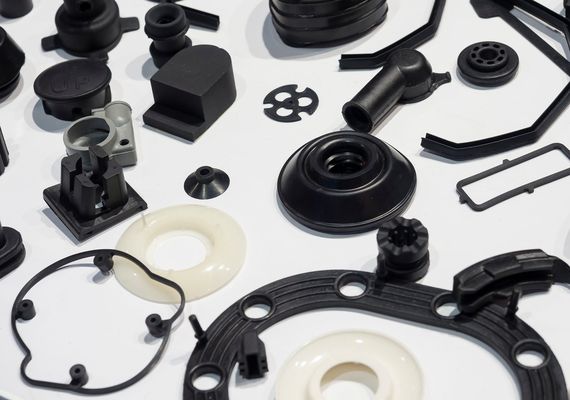
Guidelines for Designing ICF Parts and Molds
When designing parts out of carbon fiber reinforced ICF compounds, its specific physical properties need to be considered. Please refer to our Guideline for Carbon Fiber reinforced ICF Compounds for advice regarding part & mold design as well as processing. Your mold maker is not familiar with ICF compounds and unsure which kind of steel to use? Please refer to our Mold Steel Recommendations.
Disclaimer: All specifications and information given on this website are based on our current knowledge and experience. A legally binding promise of certain characteristics or suitability for a concrete individual case cannot be derived from this information. The information supplied here is not intended to release processors and users from the responsibility of carrying out their own tests and inspections in each concrete individual case. AKRO®, AKROMID®, AKROLEN®, AKROLOY®, AKROTEK®, ICX®, PRECITE® and DIA(hr)LOG® are registered trademarks of AKRO-PLASTIC GmbH.