GAS INJECTION TECHNIQUE
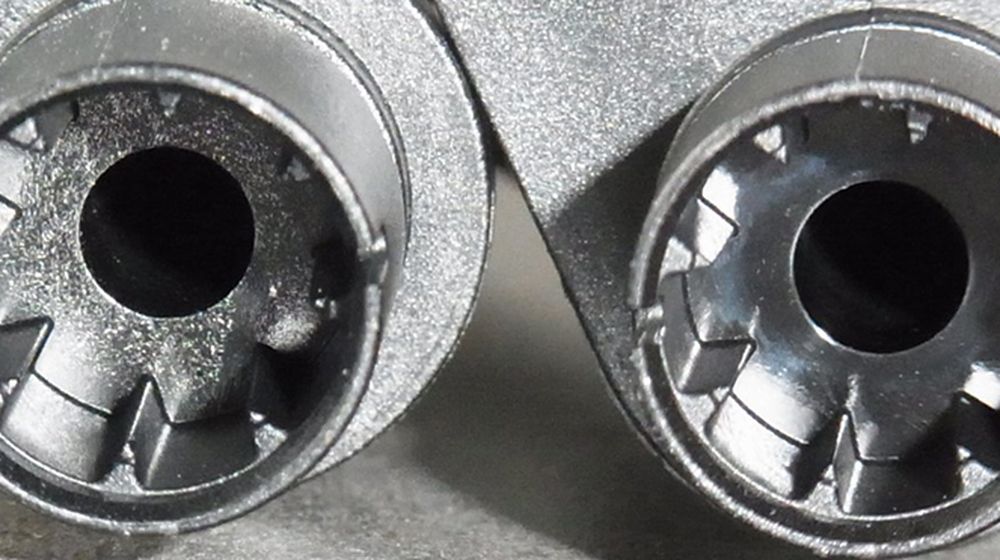
Gas Injection Technique (GIT)
The gas injection technique is the oldest and most well-established FIT variant. GIT is used to form hollow bodies as well as to compensate shrinkage effects, and occasionally as a stopgap to save unfavourable mould designs.
In this process nitrogen is typically used as an inert gas to prevent unnecessary oxidation of the plastic melts. More recent method variants from Maximator and PME use CO2 as the medium, thereby achieving further reductions in cycle time compared with the process using nitrogen. The most important step, irrespective of the selected method, remains an appropriate process design for the component and, of course, the material used. We will be happy to assist you in selecting the right method and material for your products. Due to the special methods the complexity of the process increases. Our materials are produced within such strict production tolerances that our AKROMID® WIT and GIT types ensure a stable process. In addition to our high reproducibility we also provide a wider process window with our materials.
Image dimensions not found
Change image or reupload it
A sophisticated polymer technology allows us to lower the recrystallisation point of the GIT and WIT types without negatively affecting the crystallinity. The DSC curve shows the AKROMID® GIT variant, which exhibits a recrystallization temperature nearly 15 °C lower than with identical recrystallization enthalpy. The result of this modification is beneficial for gas injection applications as well as standard injection molding applications. The component cross section pictured, illustrates the area of a valve from AFT. The glass-fiber streaks in the area of the valve seat has reduced the service life of the seal and thus failed to meet the company's stringent requirements. The surface finish requirements were only met when using AKROMID® A3 GF 15 1 GIT black (4620).
Want to Know More about Our Technologies?
Contact one of our experts and find out how we can help with your individual sector needs.
Please note that some of the methods mentioned here are patented in certain countries. Please address any queries regarding this to the plant manufacturers, who will be able to tell you which patents are covered with the purchase of the plant technology.
Disclaimer: All specifications and information given on this website are based on our current knowledge and experience. A legally binding promise of certain characteristics or suitability for a concrete individual case cannot be derived from this information. The information supplied here is not intended to release processors and users from the responsibility of carrying out their own tests and inspections in each concrete individual case. AKRO®, AKROMID®, AKROLEN®, AKROLOY®, AKROTEK®, ICX®, PRECITE® and DIA(hr)LOG® are registered trademarks of AKRO-PLASTIC GmbH.