SKI BINDINGS
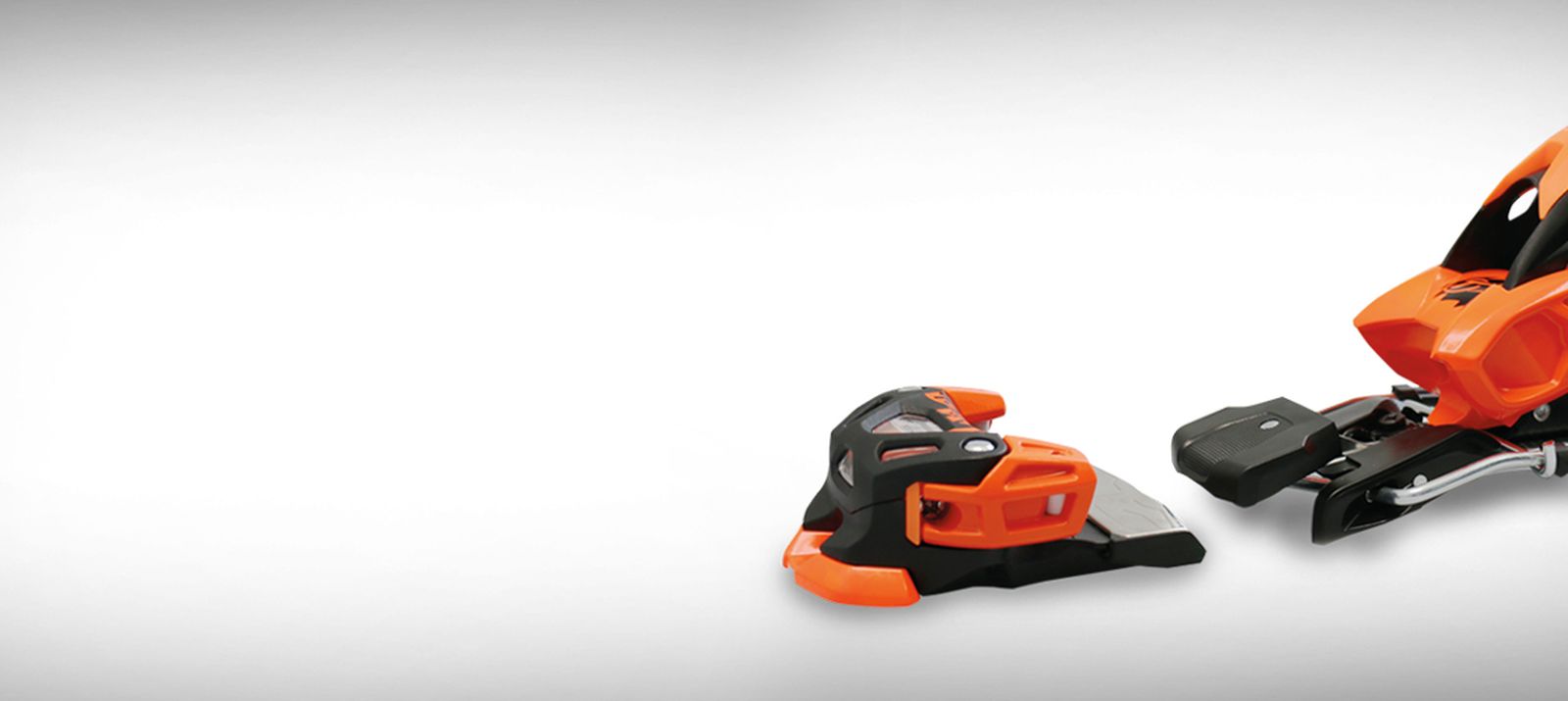
Sports & Leisure
Downhill with high-tech engineering
In many segments of the industry, especially in automotive manufacturing, engineering plastics have become standard because they are important elements for modern lightweight construction. The sports & leisure industry also places importance on the high-quality manufacturing of sport equipment and therefore complies with specifications developed by the automotive industry.
HTM Sport GmbH, based in the Austrian town of Schwechat and better known under its brand name Tyrolia, has developed a state-of-the-art production process for its ski bindings. The rapid development in the winter sports industry has raised the importance of minimising skiing injuries. In this respect, the binding is far more than a piece used to connect the boot to the ski; it is a critical factor governing safety and optimum performance in the snow. In ski production, safety components are manufactured to the tightest tolerances.
Alongside state-of-the-art production processes, high-quality raw materials are also needed to meet these strict specifications. This is why the company based in Schwechat, Austria has relied over the years on the excellent cooperation with AKRO-PLASTIC GmbH, the plastics specialists from Niederzissen in the Rhineland-Palatinate state of Germany. The company uses AKROMID® B3 GF 45 for its ski bindings, a PA 6 with 45 % glass fibre reinforcement. This is an extremely rigid material with excellent strength and toughness not only at room temperature but also when exposed to minus temperatures as required on the ski slope.
“Our customers have to be able to rely on their ski binding whatever the situation”, explains Stefan Wollner, Purchasing Manager at HTM Sport GmbH. “Only perfection provides safety!” is our motto and our guarantee to customers along the entire product life, from the initial idea to the finished ski binding and through all the manufacturing steps including the choice of material we use”.
You can find the suitable material for your application in our compound explorer.
Alongside excellent mechanical properties and good processability, parts manufactured from this material also have an outstanding surface quality which means sport product manufacturers are no longer forced to apply a final paint coating. Besides saving on both time and material, it is also safe for the environment, offering the same quality and benefits of a colored part.
This is particularly effective with minor surface damage when the ski bindings are subject to intense wear on the slope or when used on children or hire skis which have to withstand hard impacts during the ski season.
Tyrolia uses AKROMID® B3 GF 45 1 black (3851) for this ski binding for the mechanically stressed parts.
AKRO-PLASTIC delivers the properties mentioned above in part due to its innovative extrusion technology, rendered by its sister company FEDDEM GmbH & Co. KG. Both companies have worked together to develop a concept to standardise production enabling the same high standards of quality worldwide irrespective of the production site. This technology is marketed under the name ICX® Technology. Besides using identical machinery and peripherals, this technology also supports standardised processes and high-quality raw materials. Glass fibres are not only incorporated carefully, they are also distributed and homogenised in the finished compound with utmost precision.
The compounder can guarantee consistent production standards while maintaining the strictest tolerances. The Diagram plots glass fibre distribution for AKROMID® B3 GF 45 1 black (3851) over 25 batches. The average value determined from these 25 batches is 44.69 %. The current specification limits for glass fibres are +/-2.0 %, considerably below those of the competitors. “Batch to batch production” improves consistency by minimising differences between batches which in turn ensures an extremely consistent quality of parts.
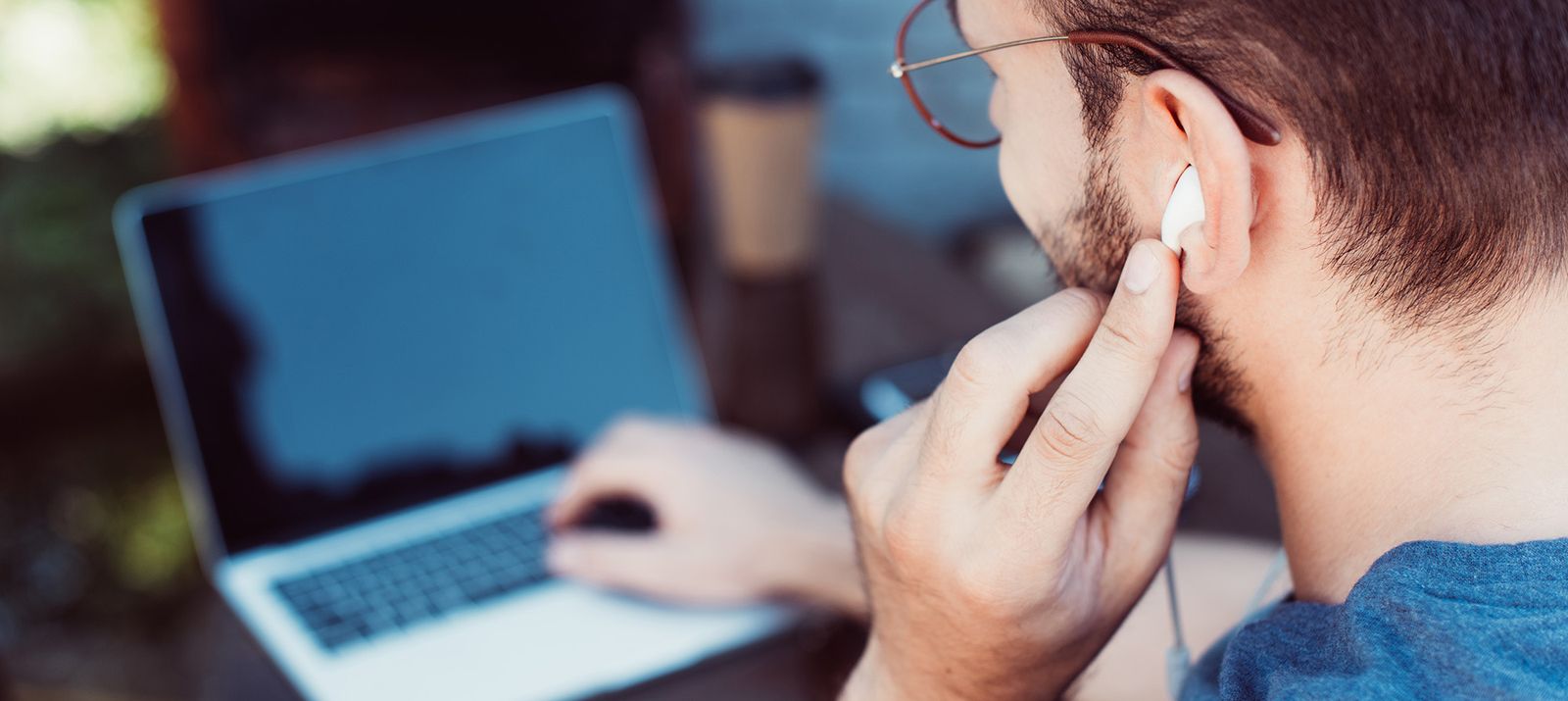