Seat bench floor KTM
)
SPE Award 2024 - 1st place in the “enabler technology” category
Seat bench floor KTM
Vehicle manufacturer: KTM Technologies GmbH
Raw material manufacturer: AKRO-PLASTIC GmbH
Tool manufacturer: Sub-Alliance / Feronyl
Machine manufacturer: Engel Austria GmbH
Parts manufacturer: KTM Technologies GmbH
Other parties involved: Leibniz Universität Hannover, Institute for Plastics and Recycling Technology
In close cooperation with Engel and other partners, KTM Technologies GmbH has developed a seat base with its GEMINUS tape sandwich technology that achieves impressive performance and environmental goals:
A weight reduction of 23%, installation space reduction of 75% and up to 85% less Global Warming Potential (GWP).
Compliance with the European End-of-Life Vehicle Regulation 2030.
Ensuring rigidity at the level of the current series component.
This is based on PP-based thermoplastic glass fiber tapes, which are applied to the top and bottom of the component where they have the greatest influence on the mechanical properties. This creates a highly rigid sandwich structure in which material can be reduced compared to the original component. The standard component was redesigned so that the tapes can be applied and maximum performance with easy handling is guaranteed. The use of glass fibers offers a good balance between performance, costs and sustainability. Due to the low thickness of the tapes of 0.2 mm, the required material input is reduced to a minimum, which keeps costs low and reduces the GWP of the component. The entire ribbed structure of the standard bench seat was eliminated by the reinforcement layers, freeing up additional critical installation space for surrounding components. To reduce the GWP, a biomass-balanced polypropylene with 10% glass fiber reinforcement based on cooking oil residues was used as the base material instead of the fossil polypropylene used as standard.
The tapes are applied via automated insertion into the mold and subsequent cold-shot injection molding in a single production step, which means that no additional heating system is required for preheating. In order to hold the tapes in position during the injection molding process, a special mold technology with a vacuum system was developed, which fixes the tapes at the edges and corners. The base material was foamed using a chemical blowing agent & precision opening for additional weight reduction. The tapes counteract the typical loss of performance caused by foaming, as well as the susceptibility to cracking due to the notches in the foamed material. At the same time, the internal stresses caused by shrinkage at the interface between the homogeneous polymer core and the tape are reduced by the foam structure. This results in stress-reduced and low-shrinkage components. Optimized process parameters based on moldflow simulation and modification of the base material ensured a tight bond between the material partners.
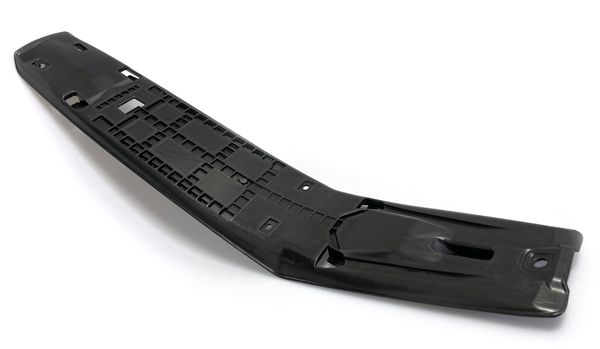
Sustainable PP with 10% long glass fiber: AKROLEN® NEXT PP LGF 10 BLACK
Geminus-Technologie
Validation was carried out using test specimens, component tests and endurance tests in accordance with KTM quality standards. Geminus technology offers an optimal basis for components that make the most of the principles of consistent eco-design in terms of reducing the material used and extending the material service life. In addition to the GWP reduction of 85%, the component can be recycled in closed-loop recycling.
Techniques used:
Tape inserts for reinforcement
Foaming with opening stroke (controlled mold opening)
Challenges
The European End-of-Life Vehicle Regulation from 2030 places new demands on the motorcycle industry with regard to the use of recycled materials and end-of-life scenarios.
The aim is to promote the circular economy and contribute to achieving the EU's environmental and climate targets. The GEMINUS technology for a new bench base meets all the requirements for closed-loop recycling. Consistent eco-design has reduced material consumption and lowered the GWP during production. Quantified analyses using Sphera's LCA software show that 27% of the GWP of the material used can be saved compared to conventional construction methods. Savings of up to 85% are possible with bio-based thermoplastic or in a closed-loop recycling scenario. A developed closed-loop recycling scenario significantly extends the material service life of the bench bases. This promotes sustainability in production, operation and at the end of the components' lives. These developments are groundbreaking for future sustainable product solutions in the motorcycle industry.