Gear wheels
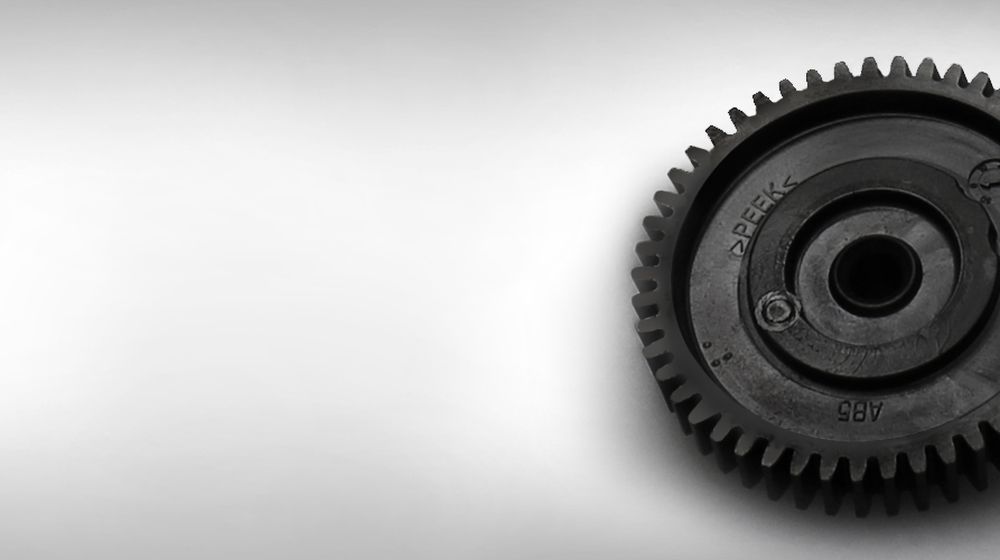
Excellent Tribological Properties
Tribological Compounds – the All-rounders of Plastics
Gear wheels and sliding elements are used in various applications in industry, the automotive sector, medical technology and also aviation in order to carry out motion changes or to transmit or adapt various speeds or torques by means of gears. As is usual in other areas, cogwheels are increasingly made of thermoplastics.
When used in the automotive industry, the focus is on reducing fuel consumption and emissions as well as increasing comfort and reducing costs. This is where thermoplastics can play off their strengths, such as lower friction losses, which lead to lower fuel consumption, low mass moments of inertia due to lightweight construction, and lower noise levels.
Compared to metal, thermoplastics can offer advantages such as low wear, noise reduction, lower weight and thus lightweight construction, economic producibility, corrosion resistance, the possibility of functional integration, emergency running properties, freedom from maintenance and more degrees of freedom in shaping, etc.
Typical materials for use as gear materials are based on polyamide, polyketone, PBT, PEEK and POM. The material properties are improved by appropriate modification using GF and CF reinforcing fibres, also in combination with various slip additives such as PTFE, graphite, aramid fibres, molybdenum disulphide or silicone oil.
You can find the suitable material for your application in our Compound Explorer.
If high power is transmitted by plastic cogwheels and they reach their load limit as a result, the gear unit may fail due to increased wear, tooth breakage or excessive noise. Typical applications are to be found in oil pumps, sensors, electric motors, steering, parking brakes, window lifters or in mass-balancing transmissions in vehicle construction, fuel pumps in the aviation industry, or printers. The requirements on the cogwheels are precision, low noise level, and resistance to environmental influences, media and temperature fluctuations.
In an automotive application, thermal management involves closing or opening the large and small cooling circuits according to the cooling water temperature. In the past, pure wax elements were often used for temperature control. This module and the much faster and more precise temperature control in the cooling circuit reduce fuel consumption and emissions, thus protecting the environment.
The temperature in the cooling water is measured and a signal is generated. This input signal acts on the corresponding module, which opens or closes the cooling circuit accordingly by means of a gear unit containing various cogwheels. Due to the correspondingly high temperatures in the automobile – between 40 °C and approx. 150 °C – and the torques to be transmitted, a metallic cogwheel acts on a cogwheel made of lubricant-modified PEEK. The output cogwheel acts on a corresponding cogwheel made of a high-temperature-resistant, reinforced polyamide. In addition to the ambient temperature, friction causes a further increase in temperature during operation.
The aim is to keep wear as low as possible over the service life. A tribologically modified PEEK specially developed by AKRO-PLASTIC GmbH is used to keep the high temperatures in a gearbox as low as possible without additional lubrication. In addition, the material offers the advantage that there is no build-up on the component or in the mould as is often the case with PTFE-modified compounds. The chosen material combination has survived the necessary tests and is being used successfully in series production.
Would you prefer to talk to us personally?
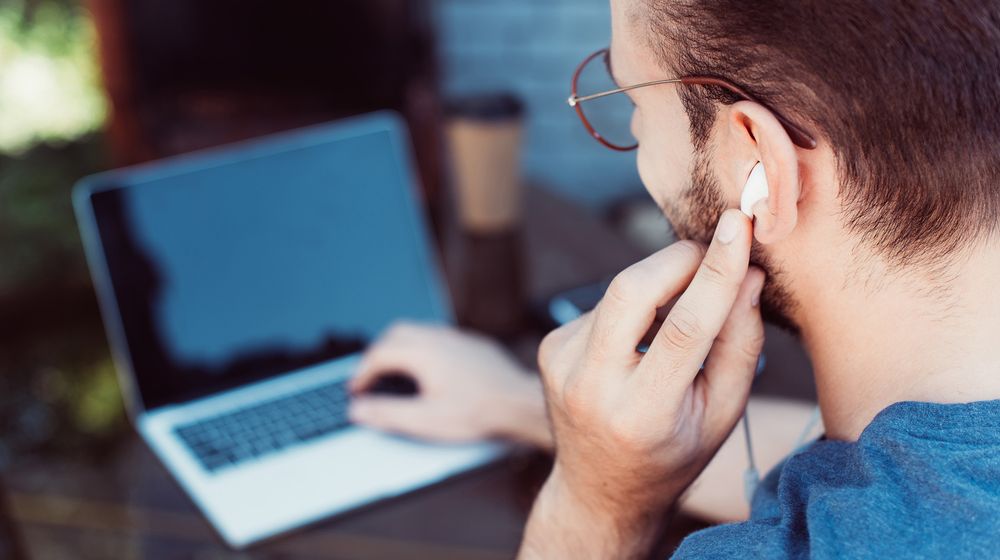