Schäumen
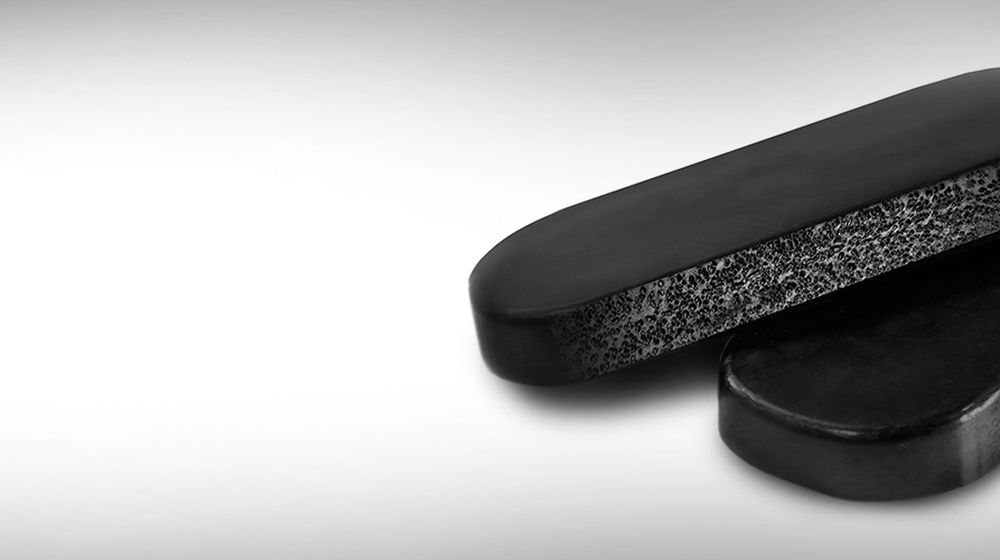
Leichter als Wasser
Motivation zum Schäumen von thermoplastischen Polymeren
Thermoplastische Polymere können physikalisch oder chemisch aufgeschäumt werden. Obwohl diese Technologie meist eingesetzt wird, um eine Gewichtsreduzierung des Bauteils zu erreichen, birgt das Verfahren vielfältige Vorteile:
Gewichtsreduzierung/Materialeinsparung
Reduktion von CO2-Emissionen
Reduzierung von Einfallstellen
Verringerung des Verzugs
Realisierung von Bauteilen mit größeren Wandstärken
Erhöhung des Steifigkeits-Gewichtsverhältnisses
Schäumprozesse
AF-Complex® TM
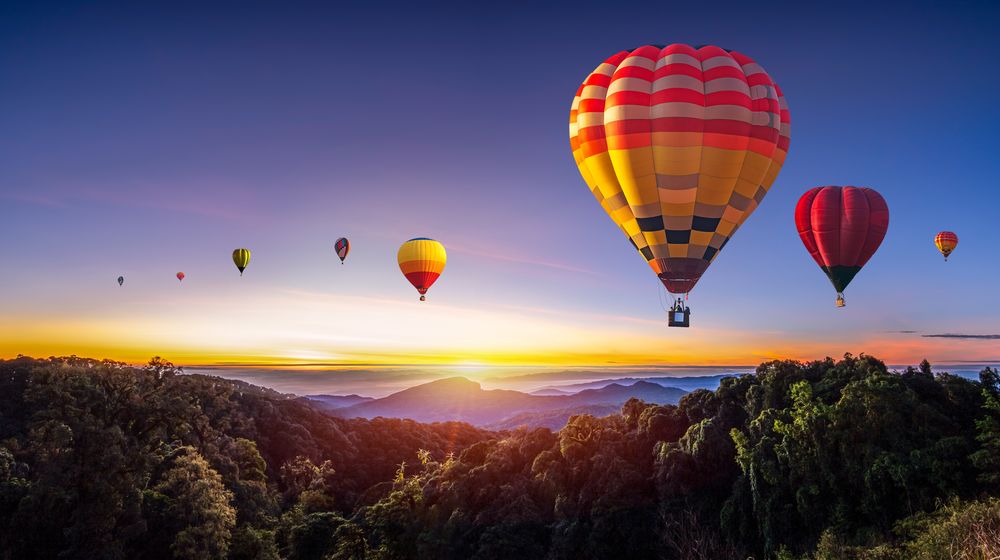
Verfahrensvarianten
Verfahrensvariante des Thermoplast-Schaumspritzgießens
Negativprägen
Negativprägen / Öffnungsprägen ist eine Verfahrensvariante des Thermoplast-Schaumspritzgießens, die wahlweise mit chemischen oder physikalischen Treibmitteln kombiniert werden kann. Das Aufschäumen der Thermoplast-Schmelze wird bei diesem Verfahren durch eine Erhöhung der Grundwanddicke des Bauteils erreicht.
Der Prozess beginnt, nachdem die Kavität komplett gefüllt wurde (Full shot). Es folgt eine sehr kurze Verzögerungszeit, damit sich eine kompakte Randschicht ausbilden kann. Anschließend öffnet die Schließeinheit das Werkzeug mittels Präzisionsöffnen bis zum gewünschten Prägehub. Nach dem Einspritzen kommt es zum Druckabfall in der Kavität und das Gas kann aus der Kunststoffschmelze austreten und somit expandieren. Durch die definierte Werkzeugöffnung verliert der Kunststoff während der Expansion nicht den Kontakt zur Werkzeugwand, wodurch sich die Schaumstruktur im Inneren ausbilden kann. Der Schäumprozess führt dazu, dass sich die Wandstärke des Bauteils während der Öffnung immer weiter bis zum Erreichen des gewünschten Prägehubs erhöht. Daraufhin folgt standardmäßig die Restkühlzeit, das Werkzeug öffnet und das Bauteil kann entnommen werden.
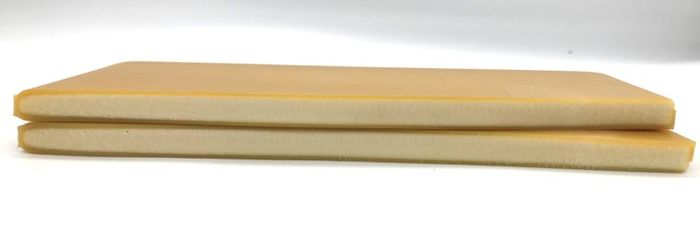
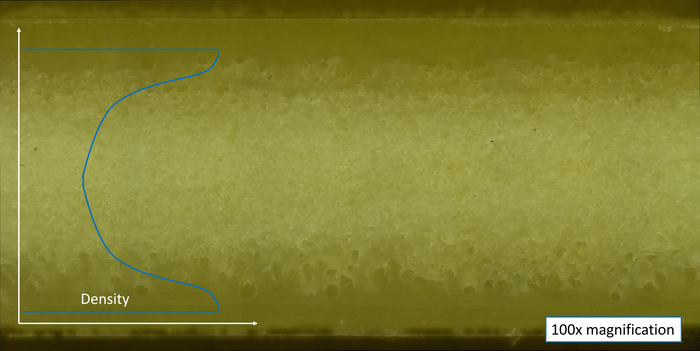
Im Negativpräge-Verfahren werden sogenannte Integralschäume erzeugt. Diese zeichnen sich durch eine kompakte, massive Randschicht mit poröser, flexibler Schaumstruktur im Bauteilinneren aus. Die Dichte des Materials nimmt somit von außen nach innen kontinuierlich ab. Daher wird das Verfahren vor allem im Bereich des Leichtbaus verwendet, z.B. für Trägerteile, Unterbodenverkleidungen etc. In diesem Bereich kann es zu hohen Zykluszeitreduktionen sowie Gewichtseinsparungen in der Größenordnung von 30 % und mehr sorgen. Es erfordert jedoch einen ganzheitlichen Ansatz - Konstruktion / Werkstoff / Fertigungstechnik - und benötigt zusätzliche Maschinenausstattung (Präzisionssteuerung für die Schließeinheit).
(Quelle: thermoPre Fachtagung 2019 „Von der Faser zum Bauteil“)
Technikum der AKRO-PLASTIC
Eine 300 t Spritzgussmaschine im Technikum der AKRO-PLASTIC ist mit dieser Steuerung ausgestattet, sodass wir bereits unterschiedliche Bauteile mit Hilfe dieses Verfahrens erfolgreich bemustern konnten. In einer Kooperation mit der Firma Arburg konnten wir beispielsweise Demonstrator Bauteile mit Integralschäumen herstellen, die bei Gewichtsreduktionen von 55 % - 60 % sowohl eine gute Schaumstruktur als auch Oberflächenqualität aufweisen.
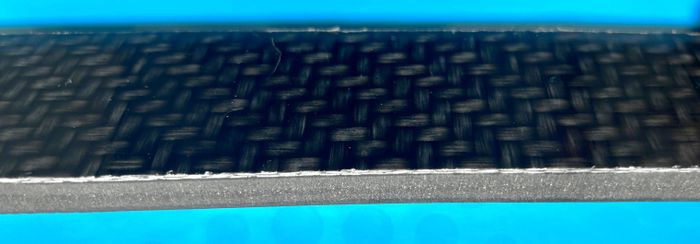
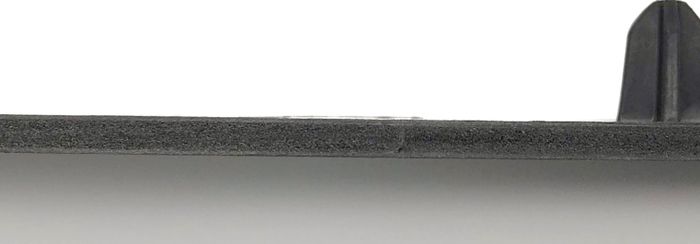
Image dimensions not found
Change image or reupload it
Gewichtsreduzierung im Negativprägen
Die Wandstärke des Bauteils bleibt unverändert
45 % Gewichtsreduzierung führt zu einer Reduzierung der Biegesteifigkeit von nur 35 %
Absolute Dichte von geschäumtem AKROMID® B3 ICF 20 (5103): 0,67 g/cm3 mit einem Biegemodul von 8400 MPa
Download
Leichter als Wasser
Wir erreichen die besten Werte der gewichtspezifischen Mechanik durch die Verwendung unserer ICF-Polymere zum Schäumen!
Image dimensions not found
Change image or reupload it
Die leichtesten Polymere von AKRO-PLASTIC
AKRO-PLASTIC hat neue Wege entwickelt, um trockene, konditionierte Kohlefasergewebe wertschöpfungssteigernd in eine Polymerschmelze einzubringen. Dabei werden die Gewebe in einem mehrstufigen Prozess so zerkleinert, dass sie wie herkömmliche Schnittkohlenstofffasern gravimetrisch auf einem Extruder dosiert werden können.
Zugversuche zeigen, dass mit leichteren ICF-Compounds von AKRO-PLASTIC auch bei höheren Temperaturen annähernd die gleichen Festigkeiten erreicht werden können wie mit deutlich höherer Glasfaserverstärkung.
Mehr anzeigen
Image dimensions not found
Change image or reupload it
Thermoplastische Polymere
Auf der Suche nach gewichtssparenden Potenzialen findet die Kunststoffindustrie kontinuierlich neue Lösungen. Durch Zugabe eines chemisch gekoppelten Polypropylens und nach Aufnahme von Wasser, weist eine neu entwickelte Polyamidmischung (PA + PP) der Firma AKRO-PLASTIC GmbH in Niederzissen die gleiche Festigkeit wie ein Standard-Polyamid auf. Je nach Anwendung und Grad der Verstärkung sparen die Blends bereits 7-10 % an Gewicht gegenüber Standard-Polyamiden und haben eine bessere Fließfähigkeit. Um das Bauteilgewicht noch weiter zu reduzieren, besteht ein Ansatz darin, die Schmelze mit einem chemischen oder physikalischen Treibmittel zu beladen.
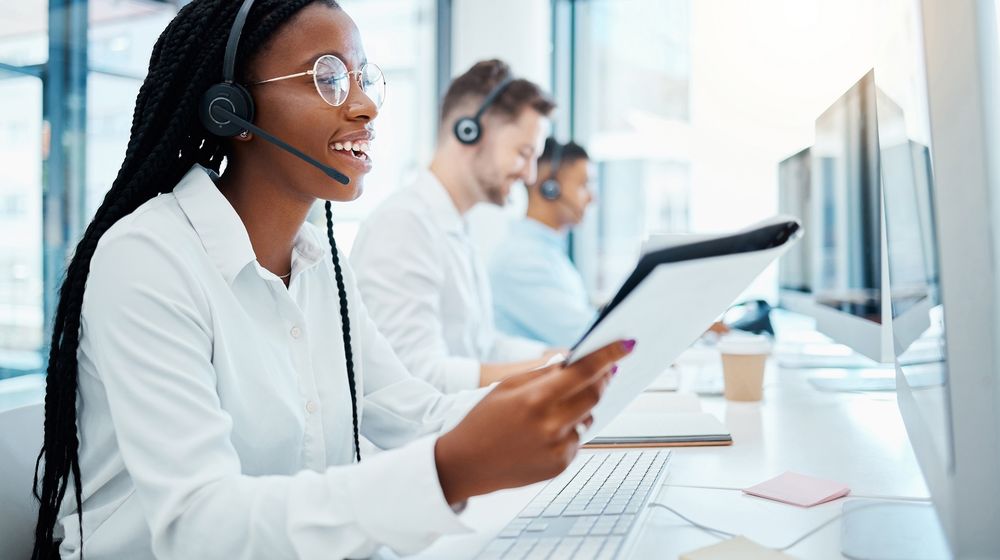